4
Control of Hazardous Noise
Hearing loss can result from exposures to high levels of occupational and nonoccupational noise. Occupational exposures are a by-product of working in close proximity to machinery and systems that are commonly used in industrialized societies. In most cases the equipment and the job of operating the equipment have been inadequately designed, so that the only way operators can perform their job is to be exposed to these noises. Nonoccupational exposures include listening to loud music, street conditions in urban areas, and other short-term and/or voluntary exposures. The main focus of this chapter is on exposures in occupational settings.
“Hearing loss due to occupational noise exposure is our most prevalent industrial malady,” according to Robert Sataloff, a prominent physician, and it affects nearly every American household (Sataloff, 1993). The hearing loss related to exposure to excessive noise, which has been known since before the Industrial Revolution, was first documented by Bernardo Ramazzini in 1713 among millers and copper-smiths (Ramazzini, 1964). The dangers have been studied for well over a century, and many laws and regulations have been passed recognizing the hazards of noise. Today, concerns include how noise exposure can also impact non-auditory health, but these effects are beyond the scope of this report.1
Very few studies have been done recently on the number of people exposed to hazardous occupational noise. In 1981 the Occupational Safety and Health Administration (OSHA) estimated that 7.9 million workers were exposed to noise levels of, or exceeding, 80 dB(A). Also in 1981, the U.S. Environmental Protection Agency estimated that more than 9 million people were exposed to daily noise levels above 85 dB(A) (EPA, 1981). Table 4-1 shows the economic sectors included in the EPA study. These numbers have probably remained stable or even increased since these studies were conducted.
TABLE 4-1 Number of Workers Exposed to Noise of >85 dB(A)
Industrial Sector |
Number of Workers |
Agriculture |
323,000 |
Mining |
255,000 |
Construction |
513,000 |
Manufacturing and utilities |
5,124,000 |
Transportation |
1,934,000 |
Military |
976,000 |
Total |
9,125,000 |
SOURCE: EPA, 1981. |
The prevalence and long history of noise exposure on the job have often led to the realization by the working population that exposure to hazardous noise is an inevitable condition of employment. Since the onset of noise-induced hearing loss (NIHL) is typically slow and not painful, workers may be more accepting of hazardous noise than of other dangers in industrial settings.
Employers today are responsible for preventing NIHL by controlling hazardous noise exposures through the use of engineering controls, by monitoring the effects of exposure on employees through the administration of audiometric exams, and by providing hearing loss prevention programs that include hearing protection devices (HPDs). However, the effectiveness of HPDs and how well they comply with workplace rules are inconsistent, at best. As illustrated in the discussion below, the difference between reductions in noise levels in the laboratory and in the “real world” can be significant.
It is generally acknowledged that most large employers administer hearing loss prevention programs, although this is not the case with most small and many medium-sized companies. The effectiveness of these programs, when provided, is often inadequate. Engineering controls to suppress
noise sources are preferred but are less commonly used. Engineering solutions and expenditures that can actually reduce noise emissions are sometimes “sold to management” by highlighting their other advantages, such as gains in productivity or quality.
The cost of NIHL can be assessed in two ways. First, there are the impacts on quality of life, such as strained relationships, difficulty or inability to communicate, feelings of isolation, lost friendships, ridicule from peers, and a general inability to relate well to others. Accidents and absenteeism also should be included in the cost of NIHL. Second is the amount of money spent on compensation for NIHL. However, studies have shown that these costs are underrepresentative of the total cost of NIHL (Shampan and Ginnold, 1982; Suter, 1990).
Data for calculating the costs are difficult to come by. In a recent study by the Institute of Medicine (IOM, 2005), it was stated that disabilities of the auditory system, including tinnitus and hearing loss, were the third most common type of disability, accounting for nearly 10 percent of the total number of disabilities among veterans. For the roughly 158,000 veterans who began receiving disability compensation in 2003, auditory disabilities were the second most common type of disability. These veterans had approximately 75,300 disabilities of the auditory system, out of a total of some 485,000 disabilities. At the end of 2004, the monthly compensation payments to veterans with hearing loss as their major form of disability represented an annualized cost of some $660 million. The corresponding compensation payments to veterans with tinnitus as their major disability were close to $190 million on an annualized basis. A 1997 study by the World Health Organization estimated that the cost of NIHL in developed countries was in the range of 0.2 to 2.0 percent of a country’s gross domestic product (GDP)—or roughly $28 billion to $280 billion for the United States (WHO, 2007). In a 2006 study in Australia, it was estimated that the real cost of hearing loss amounted to 11.75 billion AUD, or 1.4 percent of GDP (AE, 2006).
The remainder of this chapter focuses on criteria for acceptable risk of damage from hazardous noise in industry and government, hazardous noise from consumer products, research on impulsive noise, engineering controls in industry and the establishment of “buy-quiet” programs, HPDs, and the current status of HPD research.
CRITERIA FOR DETERMINING ACCEPTABLE RISK OF DAMAGE
Exchange Rate
Criteria for estimating the risk of damage from hazardous noise must be based on both the level of noise (almost always A-weighted sound pressure level) and the duration of noise exposure. In setting the level at which there is believed to be no hazard, the level at which action must be taken, and the level believed to be hazardous to hearing, it is common practice to define an exchange rate that takes into account exposure time.
Studies have shown that there is no exact value for the exchange rate (Stephenson, 2008).2 An exchange rate of 3 dB, which corresponds to equal energy,3 was first proposed by Eldred et al. in 1955. The 3-dB exchange rate, recommended by the National Institute for Occupational Safety and Health (1998a) is the most widely adopted and the most widely accepted rate by scientists (Stephenson, 2008; Suter, 1993), as well as by many government agencies in the United States, including the U.S. Department of Defense (DOD), the military services, and the National Aeronautics and Space Administration. It is also accepted by the American Conference of Government Industrial Hygienists. According to Beth A. Cooper, a member of the study committee, a 3-dB exchange rate is considered “best practice” among hearing conservation professionals (Cooper, 2009). This rate has also been standardized nationally (ANSI, 2006a) and internationally (ISO, 1990).
Not all U.S. government agencies, however, accept the 3-dB exchange rate. OSHA and the Mine Safety and Health Administration (MSHA), both part of the U.S. Department of Labor, use a 5-dB exchange rate (29 CFR 1910.95 and 30 CFR 62.0), as does the Federal Railroad Administration (49 CFR 229.121).
Using the 3-dB rate, an 85-dB level exposure for 8 hours would be considered as hazardous as an 88-dB level exposure for 4 hours. Using the 5-dB rate, the 85-dB exposure for 8 hours would be considered as hazardous as 90-dB exposure for 4 hours. As an example, it is estimated in American National Standard S3.44 (ANSI, 2006a) that an 8-hour daily exposure to 90 dB(A) would, after 20 years, result in a noise-induced threshold shift of 10 dB at 3,000 Hz for 50 percent of the population. Data for different levels, frequencies, and exposure times are given in Appendix F of the standard.
Considering the accuracy of sound-level meters and the difficulty of determining exposure over a period of eight hours, or even four hours, the difference is relatively small. However, it becomes significant for short exposure times, as shown in Table 4-2.
HAZARDOUS NOISE LEVELS IN GOVERNMENT AND INDUSTRY
For continuous hazardous noise, A-weighted sound pressure levels are used as the metric worldwide. Table 4-3 shows levels of 70 and 75 dB and higher that are known to pose some level of risk. The level in the first row (24-hour
TABLE 4-2 Hazardous Noise Exposures as a Function of Exposure Time for 3-dB and 5-dB Exchange Rates (based on exposure to 85 dB for 8 hours)
Exposure Time |
Hazardous Levels (3-dB Exchange Rate) |
Hazardous Levels (5-dB Exchange Rate) |
8 hr |
85 dB |
85 dB |
4 hr |
88 dB |
90 dB |
2 hr |
91 dB |
95 dB |
1 hr |
94 dB |
100 dB |
30 min |
97 dB |
105 dB |
15 min |
100 dB |
110 dB |
7.5 min |
103 dB |
115 dB |
TABLE 4-3 Action Points, References, and Type of Sound Level
exposure) is 5 dB below the level in the second row (8-hour exposure; 10 log10{8/24} = –5 dB). This corresponds to a 3-dB exchange rate. Because sound pressure levels vary with time, the levels in the table are generally time-weighted averages (TWAs). OSHA and MSHA, however, have their own methods of calculating noise dose (29 CFR 1910.95, 30 CFR 62.0).
The International Institute of Noise Control Engineering (I-INCE) has studied regulations on exposure to noise worldwide (I-INCE, 1997). An updated version of the I-INCE data is shown in Table 4-4 (Suter, 2006). As the table shows, an 8-hour average A-weighted sound pressure level of 85 dB and a 3-dB exchange rate is used in many countries. The original references for the table are given in Suter (2006).
HAZARDOUS NOISE FROM CONSUMER PRODUCTS AND LEISURE ACTIVITIES
Noise from consumer products can sometimes be as hazardous as occupational noise in the workplace. In both cases the degree of hazard depends on noise level and exposure time. One major difference is that noise in the workplace tends to come from a number of sources, whereas noise from the products discussed in this section tends to come from a single source. When exposure to occupational noise is added to exposure to noise during a leisure activity, the degree of hazard increases.
Consumer Products
Noise from consumer products and other hazardous sounds can be generated by a variety of sources, including kitchen appliances, audio systems, power tools (both handheld and stationary), and all types of yard equipment. High levels of noise from these products and long exposure times can contribute to the risk of NIHL from occupational noise. It is reasonable to assume that the 3-dB exchange rate applies to exposures longer than 8 hours, from either or both. Noise levels from a variety of consumer products, including toys, have been published by Schwela (2006).
Recreational Noise
Sources of hazardous recreational noise include on-road and off-road vehicles, loud music at concerts, and small aircraft engines. Like exposure to noise from consumer products, the degree of risk depends on the sound pressure level and exposure time, as well as the amount of noise exposure in the workplace.
Noise from Personal Listening Devices
Personal listening devices are known to emit sound pressure levels that can be hazardous, if they are abused. It has been estimated that at least 5 percent of users of these devices
TABLE 4-4 Worldwide Regulations for Exposures to Hazardous Noise in the Workplace
Nation, Date (if available) |
PEL (8-hr average) dBA |
Exchange Rate dBA |
dBA Level for Engineering Controls |
dBA Level for Audiology Tests and Other HC Practices |
Comments |
Argentina, 2003 |
85 |
3 |
85 |
85 |
|
Australia, 2000 |
85 |
3 |
85 |
85 |
Notea |
Brazil, 1992 |
85 |
5 |
85 |
|
|
Canada, 1991 |
87 |
3 |
87 |
84 |
|
Chile, 2000 |
85 |
3 |
|
|
|
China, 1985 |
85 |
3 |
85 |
|
|
Colombia, 1990 |
85 |
5 |
|
|
|
European Union, 2003 |
87 |
3 |
85 |
85 |
|
|
|
|
|
80 |
|
Finland, 1982 |
85 |
3 |
85 |
|
|
France, 1990 |
85 |
3 |
|
85 |
|
Germany, 1990 |
85 |
3 |
90 |
85 |
|
Hungary |
85 |
3 |
90 |
|
|
India, 1989 |
90 |
|
|
|
|
Israel, 1984 |
85 |
5 |
|
|
|
Italy, 1990 |
85 |
3 |
90 |
85 |
|
Mexico, 2001 |
85 |
3 |
90 |
80 |
|
Netherlands, 1987 |
80 |
3 |
85 |
|
|
New Zealand, 1995 |
85 |
3 |
85 |
85 |
|
Norway, 1982 |
85 |
3 |
80 |
|
|
Spain, 1989 |
85 |
3 |
90 |
80 |
|
Sweden, 1992 |
85 |
3 |
85 |
85 |
|
United Kingdom, 1989 |
85 |
3 |
90 |
85 |
|
United States, 1983 |
90 |
5 |
90 |
85 |
|
Uruguay, 1988 |
85 |
3 |
85 |
85 |
|
Venezuela |
85 |
3 |
|
|
|
NOTE: PEL is the permitted exposure level in each country. dBA rather than dB(A) is used because it was used in the referenced table. aEach Australian state and territory has its own legislation for noise, but all have now adopted the 8-hour PEL of 85 dBA and the 3-dBA exchange ate (ER). bDespite the existence of a Canadian national standard, there is some variation among the standards in individual provinces: Ontario, Quebec, and New Brunswick use 90 dBA with a 5-dBA ER; Alberta, Nova Scotia, and Newfoundland use 85 dBA with a 5-dBA ER; and British Columbia uses 85 dBA with a 3-dB ER. Most require engineering controls to the level of the PEL. Manitoba requires certain hearing conservation practices above 80 dBA, hearing protect ors and training on request above 85 dBA, and engineering controls above 90 dBA. cThe European Union (EU; Directive 2003/10/EC) puts forward three exposure values: an exposure limit value of 87 dBA; an “upper action” level of 85 dBA; and a “lower action” level of 80 dBA, all using the 3-dBA ER. The attenuation of hearing protectors may be taken into account when assessing the exposure limit value but not for requirements driven by the upper and lower action values. At no time shall an employee’s noise exposure exceed the exposure limit value. When exposures exceed the upper action level, the employer must implement a program of noise reduction, taking into account technology and the availability of control measures. dEU continued: Hearing protectors must be made available when exposures exceed the lower action value of 80 dBA. Hearing protectors must be used by workers whose exposures equal or exceed the upper action value of 85 dBA. Audiometric testing must be available to workers whose exposures exceed the upper action value, and when noise measurements indicate a risk to health, these measures must be available at the lower action value. eThe German standard (UVV Larm-1990) states that it is not possible to give a precise limit for the elimination of hearing hazard and the risk of other health impairments from noise. Therefore, the employer is obliged to reduce the noise level as far as possible, taking technical progress and the availability of control measures into account. fIndia: This is a recommendation, not a regulation. gThe Netherlands’ noise legislation requires engineering noise control at 85 dBA ”unless this cannot be reasonably demanded.” Hearing protection must be provided above 80 dBA, and workers are required to wear protection devices at levels above 90 dBA. hThese levels apply to the OSHA noise standard, which cover workers in maritime and general industries. The U.S. military has more stringent standards; DOD as a whole uses the 85-dBA PEL and the 3-dBA exchange rate. The Air Force and Army have similar requirements, and the Navy is about to adopt the 3-dB ER. |
are exposed to A-weighted TWA levels of greater than 85 dB (Fligor, 2008).4 Considering the very large number of such devices sold, and the frequent long exposure times, it has been estimated that 50,000 people develop NIHL from listening to such devices for more than 4 hours per day over a period of years (Fligor, 2009; SCENIHR, 2008). Recommendations for avoiding NIHL are listed below (Fligor and Cox, 2004):
-
Limit listening level to 60 percent of the maximum volume.
-
Limit listening time to 1 hour.
-
Use a lower gain setting and shorter listening times when over-the-ear rather than in-ear earphones are used.
Exact limits are difficult to specify because the sensitivity of earphones varies with the manufacturer and because different earphones can be used with the same amplifier. Assessments of NIHL caused by personal listening devices have also been made in Switzerland (Hohmann et al., 1999) and the Netherlands (Passchier-Vermeer, 1999).
Noise from Toys
A survey of toy safety standards for noise levels (ASTM, 2008) and recommendations have been published by the U.S. Public Information Research Group (PIRG, 2005). Another survey that includes epidemiological studies as well as various national and international activities is available (Altkorn et al., 2005). The League for the Hard of Hearing provides examples of noise levels from toys (LHH, 2009). A report by the Institute of Sound and Vibration Research provides measurement data and recommendations about noise from toys (ISVR, 1997); for example, the recommendation for the C-frequency weighted instantaneous sound pressure level from cap-firing toys is that it not exceed 120 dB when measured 25 centimers from the ear and 125 dB when measured 2.5 centimers from the ear. Contrast this with an undated alert from the U.S. Product Safety Commission (CPSC, 2001a) that states, “CPSC reminds parents that caps may also pose a noise hazard. A current CPSC regulation limits the decibel level of caps to no more than 158 decibels. A warning label is mandatory on caps in the 138 to 158 decibel level as follows: WARNING—Do not fire closer than 1 foot to the ear. Do not use indoors.” See CPSC (2001b) for the full requirement. The measurement method is specified in 16 CFR 1500.47.
IMPULSIVE NOISE
Physical Characteristics
In contrast to continuous noise, impulsive noise comes in many different forms and is much more difficult to describe. Impulsive noise may consist of a single burst, such as impact noise generated by a hammer hitting a nail, a sonic boom, or a single rifle shot. It may also consist of a series of bursts, either closely spaced or more or less isolated—such as a series of hammer blows. Thus, characterizing a particular impulsive noise has been a subject of interest to engineers for many years (IEEE, 1969). Characterizing impulsive noise and associated auditory hazards was the subject of a NIOSH workshop in 2005 and two presentations at a workshop sponsored by the National Academy of Engineering (NAE) in August 2008 (Dancer, 2008; Murphy, 2008).5,6
Physical measures of an impulsive noise depend on its character, and relating the degree of auditory hazard to a physical measure is a complex undertaking. For a single burst of noise, the instantaneous sound pressure is usually of most interest. However, measuring it requires a system with a wide frequency response, a wide dynamic range, and a small phase shift.
A conventional sound-level meter with a peak-reading circuit and C-weighting can provide a reasonably good measure of the peak value of the instantaneous sound pressure, and this peak value, expressed in decibels, has been widely used as a damage risk criterion. However, peak values cannot be measured using the fast or slow dynamic characteristics of a sound-level meter because of their long time constants. Also, A-frequency weighting does not satisfy the criterion of a wide bandwidth.
At one time, an impulse sound-level meter was standardized. The instrument had a time constant believed to approximate the loudness of a transient sound and a decay time constant long enough to obtain a peak reading. However, standards committees discouraged use of this meter, and it is no longer standardized.
Another quantity that can be measured with a sound-level meter is sound exposure, which is the integral of the squared instantaneous pressure over the duration of the burst. Expressed in decibels, this becomes the sound exposure level, which has been used to characterize, for example, aircraft flyovers. The relationship to auditory hazard is discussed in the next section.
One parameter that cannot be measured with a conventional sound-level meter is the A-duration (unrelated to A-frequency weighting). A-duration is the time from the beginning of the burst to the time that the instantaneous sound pressure is 20 dB below the peak value. A-duration and other characteristics of impulsive noise are described in an American National Standard (ANSI, 2006b).
For a series of bursts or for continuous noise with an impulsive component, two other parameters are of interest. The peak and root mean square sound pressure can be measured, and the ratio, expressed in decibels, is the crest factor. Impulsive noise is characterized by a crest factor higher than that of random noise, which is why a system with a wide dynamic range is necessary for making accurate measurements. High crest factors are related, in a statistical sense, to the ratio of the fourth moment and second moment about the mean
of the signal (kurtosis). Although not widely used, kurtosis is a measure of the impulsiveness of noise.
Auditory Hazard
The peak value of the instantaneous pressure, expressed in decibels and with C-frequency weighting, has been widely used as a measure of auditory hazard for impulsive noise. For example, OSHA has set a limit on the peak sound pressure level: “Exposure to impulse or impact noise should not exceed 140 dB peak sound pressure level” (OSHA, 1971c).
The European Union sets an upper limit of 200 Pa (1 Pa = 1 N/m2) for instantaneous sound pressure using C-frequency weighting (EC, 2003). This limit is not expressed in decibels, presumably to avoid confusion with the lower limits for continuous noise. The 200-Pa peak sound pressure can be converted to a sound pressure level: 10 log (p2/pref2) = 140 dB, where the reference pressure, pref, is 20 micropascals.
World Health Organization guidelines state that peak sound pressure levels should not exceed 140 dB(A) for adults and 120 dB(A) for children (WHO, 1999). Note the use of A-frequency weighting in this case.
The use of peak sound pressure level as a measure of auditory hazard was questioned by Dancer at an NAE-sponsored workshop (Dancer, 2008). He showed data from French military studies comparing auditory hazard from howitzer and rifle rounds. Soldiers were exposed to 20 rounds at the same peak sound pressure level (159 dB) but with an A-duration of 9 and 0.25 milliseconds, respectively. Almost no temporary threshold shift (TTS) was observed for the howitzer rounds, but significant TTS was found for the rifle rounds. Since it is generally accepted that repeated exposure to noise that causes TTS leads to permanent threshold shift, these results lead one to question the peak level and emphasize the importance of the A-duration in determining auditory hazard. They also show that very high sampling rates are necessary when recording digital samples of a short burst of noise.
Because impulsive noise can be a series of bursts or continuous noise with an impulsive component, the question is whether such noise, generally recognized by its high crest factor, has the same auditory hazard as continuous noise when the two have the same A-weighted sound pressure level. This question has been raised for more than 30 years.
Brüel (1977) asked if damaging noise was being measured correctly. He noted that studies at the time showed that industrial noise, presumably with an impulsive component, appeared to be more damaging than music at a higher noise level. Similarly, he noted that pilots with no ear protection in certain airplanes do not suffer as much hearing loss as pilots who listen to radio communications with their attendant clicks and bursts. This suggests that the peaks in the time waveform are significant contributors to auditory hazard.
NIOSH (1998b) cites a number of studies that indicate that impulsive noise is more dangerous than continuous noise of the same level. However, NIOSH also cites studies that show that the equal energy rule adequately predicts hearing damage. Therefore, at these levels impulsive noise, even when superimposed on a background of continuous noise, can probably be treated similarly to continuous noise for the purposes of assessing auditory hazard.
Dancer (2008) presented results from a number of studies of hearing damage (i.e., Price 2007) and concluded that an 8-hour, A-weighted equivalent level of 85 dB (LAeq8) should be used as the damage risk criterion for both continuous and impulsive noise, whether military or occupational. If this conclusion is accepted, it would extend the equal energy concept for hazardous noise to even very short bursts of noise, which would greatly simplify the determination of auditory hazard. The sound exposure of an impulse would be determined, averaged over an 8-hour time interval, and compared with current damage risk criteria for continuous noise.
Another approach to assessing auditory hazard from impulsive noise is the Auditory Hazard Assessment Algorithm for Humans (AHAAH), developed by G.R. Price for the U.S. Army (U.S. Army Research Laboratory, 2010). This mathematical model of the human auditory system requires as input the incident sound pressure as a function of time. An assessment of this model is well beyond the scope of this report. We simply note that Dancer (2008) suggested it be used as a laboratory tool to clarify some specifics of weapons noise. Dancer also concluded that the AHAAH model provides better estimates of auditory hazard than LAeq8 for the sound of air bags and high-level noise.
In the preceding discussion of physical characteristics of impulsive noise, kurtosis was identified as another measure of the impulsiveness of noise. Recent data from a series of animal experiments and at least one epidemiological study indicate that the kurtosis metric, with possible adjustments for frequency spectrum and bandwidth, in combination with equal energy would be an effective predictor of the traumatic effects of complex noise (Davis et al., 2009; Zhao et al., 2010).
The study committee concluded that damage risk criteria for impulsive noise need further study and that such studies and an agreement in the international standards community on optimal damage risk criteria for impulsive noise should serve as a basis for changing national, European Union, and international criteria for assessing auditory hazard from impulsive noise. Such studies will require the participation of both engineers and experts in the physiology of the ear. Military experience will be a very valuable input to the process.
ENGINEERING CONTROLS
HPDs and hearing protection programs are not the best way to protect the hearing of workers. The preferred way, often called “engineering controls,” is to reduce workers’ exposure by reducing the noise of the machinery or equipment that generates the noise. If it is not possible to reduce
the noise from the source, then noise control along the path by which the noise propagates to workers, such as inserting a noise control element between the machinery and workers, can be used.
However, the most effective way, indeed, perhaps the only way, to eliminate NIHL from occupational noise exposure is well-designed engineering controls, which are permanent, are effective with or without worker/supervisor compliance, reduce absenteeism, make communication easier, reduce worker compensation costs, and reduce legal costs. For all of these reasons, engineering controls are the protection method of choice according to OSHA and MSHA.
Noise Mechanisms
The main differences between noise generated by industrial machinery and noise generated by other sources are size, complexity, and diversity. Compressors, for example, can be as small as a compact refrigerator or enormous, with a footprint of 20 × 30 feet. The main sources of noise are fluid flow, friction, magnetic forces, mechanical forced vibration, impact, and combustion.
Noise from fluid flow is generated by the movement of air (e.g., intake or exhaust air for engines, compressed air used to clean off a workbench), gas (e.g., process gas flowing through valves and piping), and liquids (e.g., fluid flow through pipes and valves). Mechanical vibration includes noise radiated from machinery casing compressing air or gas or pumping liquid. It includes noise radiated from surfaces mechanically attached to a noise source.
Friction sounds can be characterized as stick-slip sounds, like the screech of Styrofoam cups on a table top, chalk on a blackboard, or the squeal of tires when brakes are applied sharply; rubbing sounds, like sanding on a surface or pistons moving inside cylinders in an engine; and rolling friction, like ball bearings or tire noise. Sounds generated by magnetic forces can be emitted from electrically powered equipment, such as transformers, motors, and circuit breakers. Typically, these noises have strong tonal components.
Impact tools, like pneumatic chippers, generate impact noise when the equipment impacts the surface, but the response of the surface to the impact often dominates what is heard. Chipping on a rubber surface is obviously much quieter than chipping on a metal plate. Combustion noise, such as noise from a furnace or the sound from the ignition of fuel inside a gasoline or diesel engine, has strong low-frequency components.
Industrial machines have drivers (i.e., power sources), such as electrical, compressed air, or hydraulic motors; gasoline or diesel engines; or gas or steam turbines. The power sources drive blowers, fans, compressors, pumps, and countless other mechanisms.
Depending on the application, a gearbox might be placed between the power source and the driven equipment. An example of a complex noise source might be a compressor driven by an electric motor. These two items would probably be mounted on a metal frame called a skid. The noise sources would be those of the motor (including a cooling fan, motor casing that radiates magnetic and mechanical noise, and a skid that radiates structure-borne noise), and the compressor (including intake and discharge air, intake and/or discharge piping, engine casing of the compressor, and a supporting structure).
This brief description of noise sources illustrates that industrial equipment often has numerous sources of noise. Thus, noise control requires controlling the most powerful noise component first and then treating all of the other components in turn. For example, on a large fan with an open intake, the intake noise is dominant. Once the intake has been appropriately silenced, it is necessary to review other sources, such as the cooling fan for the motor, the casing-radiated noise of the fan and motor, and possible structure-borne noise from the skid.
Engineering Controls
Some engineering controls (Bruce, 2007) modify the noise source to reduce the amount of radiated noise. This can be accomplished in several ways:
-
modifying the source so that it produces less noise
-
changing the operating parameters so that less noise is generated
-
adding mufflers or silencers to intakes and exhausts
-
providing damping to reduce vibration
-
isolating vibration to reduce excitation of other structures
-
providing acoustical shielding from the source
-
enclosing the source with lagging or a partial or total enclosure
A number of “obvious” engineering controls can usually be implemented in existing facilities to address 25 to 33 percent of noise problems in most workplaces (Driscoll, 2008).7 Some are so obvious that they can easily be overlooked. Nevertheless, although these controls can be easily stated, their application requires careful selection. Some “obvious” controls are listed below:
-
Maintain equipment properly (e.g., fix steam or air leaks). In operations that require high-pressure steam, steam leaks are often the dominant noise source.
-
Change operating procedures (e.g., relocate the operator and controls to a quieter position).
-
Replace equipment (e.g., buy a quieter version of the product).
-
Modify the room (e.g., install sound absorptive materials). If the noise source and worker are some distance apart, sound absorption in the intervening space can reduce noise in the reverberant field.
-
Relocate equipment (e.g., put noisy equipment in areas that are often unoccupied).
-
Use equipment at proper operating speed (e.g., the higher the speed, the louder the noise; run equipment at the lowest practical speed).
Noise from Fluid Flow
Noise sources with fluid flow include fans, compressors, engines, pumps, and valves. Controls for reducing intake and discharge noise include lining ducts, installing dissipative and reactive silencers, and installing special-purpose silencers.
The inlet or exhaust duct can be lined with a sound-absorbent material, such as fiberglass or mineral wool. Typical thicknesses range from 1 to 4 inches, depending on the strength of the low-frequency component. Dissipative silencers also use sound-absorbing materials to attenuate noise. A simple dissipative silencer might be a set of parallel baffles running lengthwise to direct airflow and reduce noise. The absorptive material might be mineral wool or fiberglass covered with glass fiber cloth to reduce erosion from airflow. In addition, a perforated or expanded metal facing could be added to the material to protect against contact damage. The longer the baffles and the closer they are together, the more effective they are as silencers. Reactive silencers operate on the principle of mismatching acoustic impedance. A change in acoustic impedance causes a portion of the sound energy to be reflected back to the source or back and forth within the silencer.
Special-purpose silencers are available to fit exhaust ports on pneumatic equipment, air wipes, and parts blowoffs. Recently, an innovative silencer called a duct resonator array (DRA) was developed based on the principles of a Helmholtz resonator (Liu, 2003). DRAs positioned at the diffusers in larger centrifugal compressors effectively reduce noise levels from these machines; DRAs can also be placed in discharge piping in a pipe spool. Basically, they reduce the A-weighted sound pressure level by at least 10 dB—which is similar to “halving” the loudness of the sound.
Lagging is a noise control treatment that consists of layers of treatment around piping to reduce radiated noise in refineries and noise from forced-draft and induced-draft fan ducts. The first layer wrapped around the pipe consists of glass fiber or mineral wool, typically 2 to 4 inches thick and 6 to 8 pounds per cubic foot. Next a mass-loaded vinyl layer weighing 1 to 2 pounds per square foot is wrapped around the glass fiber or mineral wool. The outer layer is a weather-proof covering. Depending on the details of the installation, lagging can reduce the A-weighted sound pressure level by 10 to 20 dB.
Radiated Noise from Machine Housings
Airborne noise can be radiated by any surface. For example, consider a piano. The keys strike hammers that strike the strings. The strings do not produce much sound by themselves, but they are attached to the much larger sound board that radiates the sound. In general, the larger the vibrating panel, the greater the sound radiated from the surface.
Another example is a parts bin into which metal parts are dropped. If the bin is made of perforated metal, the radiating area is smaller than if it is made of solid metal; thus, the level of radiated sound will be lower. Of course, materials with high internal damping radiate even less noise. If the bin were made of rubber (which has high internal damping), rather than metal (which has low internal damping), it would radiate even less sound.
Sometimes machinery is housed inside an enclosure provided by the original equipment manufacturer. In such situations it is desirable for the panels of the housing to be appropriately treated. Damping compound should be applied to the panels if there is any possibility that the resonance frequencies of the panels will be excited. If the machine inside the enclosure produces significant vibration into the enclosure housing and structure, the panels should be vibration isolated from the structure. In addition, it may be useful for the machinery enclosure to be mounted on vibration isolators to keep it from transmitting vibration to the floor.
Machinery Shields, Outdoor Barriers, and Enclosures
Shields. An acoustical shield may be inserted between the worker and a noisy section of a machine. Shields are often mounted directly on the machine and reduce noise by 8 to 10 dB under the following conditions:
-
The worker is near the noisy operation.
-
The smallest dimension of the shield is at least three times the wavelength of the dominant noise.
-
The ceiling above the machine is covered with sound-absorptive material.
Shields can be manufactured from safety glass, one-quarter-inch clear plastic, metal, or wood. Durability, expense, need for visual observation of the operation, and need for access to the operation should all be considered in selecting a material. If possible, oil-resistant, cleanable, sound-absorptive materials should be incorporated into the machine side of the shield.
Outdoor Barriers. Any solid impervious wall that blocks the line of sight between a noise source and an observer will reduce the noise level at the observer. The reduction depends on the frequency of the noise, the distance of the source from the barrier wall, the distance of the receptor from the barrier wall, and the height of the wall. Low-frequency
sound diffracts around the ends of the wall and over the top more readily than high-frequency sound. Thus, the wall has lower values of attenuation for low-frequency sound than for high-frequency sound. Typically, low-frequency sound is attenuated by less than 5 dB, whereas high-frequency sound can be attenuated by as much as 20 dB.
Partial Enclosures. A partial enclosure is a series of walls around a machine with the top left open. A partial enclosure can be effective inside a plant if located near a wall. However, some noise will still radiate out the top and contribute to the reverberant sound in the room. Reflections from the ceiling will increase the sound pressure level at distances farther from the enclosure. A sound-absorptive ceiling can reduce reflected sounds and thereby increase the effectiveness of the enclosure. For maximum effectiveness, the sound-absorptive ceiling should extend out to the location of the receivers. Sound-absorptive materials should also be applied to the inside of the enclosure walls.
For equipment handling flammable liquids/gases, appropriate fire-retardant systems and alarms will be required.
Total Enclosures. A total enclosure with a closed top provides better noise reduction than a partial enclosure. However, openings are usually necessary to provide (1) access by personnel, either for inspection, maintenance procedures, or operator usage, or (2) access to (or for) materials, such as raw materials, products, or scrap.
Sound leakage around doors, windows, and hatches make enclosures much less effective. Leaks can be handled with properly sealed doors, windows, and hatches. Closed-cell, elastomeric weather stripping with a pressure-sensitive adhesive can be effective seals. Special acoustical gaskets are available, as well as magnetic-strip gaskets similar to those used on refrigerator doors.
If workers must have visual access to machines, lighting may be required. If workers use the sound of the machinery to evaluate its performance, it may be necessary to retrain them or to place a rugged microphone inside the enclosure and send the signal to a small adjustable loudspeaker at the worker’s position. Occasionally, it is possible to develop processors that incorporate the worker’s knowledge to automatically adjust the machinery for optimal performance. Openings for raw materials, product, and scrap flow can be tunnels lined with sound-absorptive material. The noise reduction will depend on the length and cross section of the tunnel, as well as the thickness of the sound-absorptive material.
Ventilation is required for all total enclosures and some partial enclosures. Ventilation openings can be acoustically lined ducts, elbows, or mufflers, depending on the severity of the problem.
Enclosure panels and structures should not contact any part of the machinery. If the enclosure is mounted on the machinery, it should be vibration isolated.
Advantages of Designing for Noise Control
Good industrial hygiene (as well as common sense) involves removing hazards. In addition, workers may need personal protective equipment. For example, steel-toed shoes may protect workers from unexpected events, such as a large casting falling on a worker’s foot. The same precautions should be taken to protect workers’ hearing. Protecting hearing should not require constant intervention on the part of the worker, such as wearing earplugs or other HPDs. Workers’ hearing can be protected by engineering controls designed into equipment or even added after the fact. With engineering controls, the noise level remains constant, whereas with HPDs, protection is dependent on the availability and proper selection of the HPD, proper training of the worker, proper action by the worker, and appropriate supervision.
Controlling noise in the workplace has many advantages, such as reducing absenteeism, improving communication among workers, reducing the number of accidents, improving efficiency, and increasing productivity. The two examples below show how designing engineering controls into a system can lead to process improvements. Both of these companies worked with their suppliers to develop engineering controls, which they then purchased.
An automobile company used a procedure published by the Association for Manufacturing Technology (formerly the National Machine Tool Builders Association) to measure noise levels in its facilities (AMT, 2006) and then proceeded to use engineering controls to control the noise. In one instance the company replaced some equipment in its metal assembly weld cells. According to Robert Anderson, an acoustical consultant, “Replacing pneumatic drives with servo drives has reduced noise from spot weld impacts, while extending weld tip life and saving energy” (Anderson, 2008).8
Michael Bobeczko, director of marketing, Sukut Construction, documented improvements in production that resulted from noise control measures in the manufacturing equipment industry (see Table 4-5). He described a typical manufacturing facility (Bobeczko, 1978).9
A process line in a typical aluminum can plant produces approximately 800 cans per minute. This high-speed process starts at a cup press where sheet aluminum is blanked and drawn into cups. The cups are distributed to bodymakers where each machine redraws and irons the cup into a long seamless can. The can is then usually trimmed to a specific height and conveyed to a washer where it is cleaned, chemically treated and dried. The can exterior is decorated by dry offset methods and the can interior is sprayed with a protec-
TABLE 4-5 Noise Reduction and Productivity in a Beverage Can Manufacturing Plant
Manufacturing Equipment |
A-Weighted Sound Pressure Level at 1 meter (dB) |
Operating Speed in Cans/Minute |
|||
Before |
After |
Noise Reduction |
Before |
After |
|
Conveyors |
110 |
77 |
33 |
600 |
2,400 |
Body maker |
104 |
82 |
22 |
120 |
240 |
Trimmer |
102 |
80 |
22 |
120 |
250 |
Necker/flanger |
105 |
85 |
20 |
600 |
1,100 |
Scrap conveyor |
105 |
80 |
25 |
600 |
2,400 |
SOURCE: Bobeczko, 1978. |
tive coating. The last forming operation necks and flanges the open end of the can.
These same results might be possible through regulation (Porter and van der Linde, 2005):
[R]egulation creates pressure that motivates innovation and progress. Our broader research on competitiveness highlights the important role of outside pressure in the innovation process, to overcome organization inertia, foster creative thinking and mitigate agency problems. Economists are used to the argument that pressure for innovation can come from strong competitors, demanding customers or rising prices of raw materials; we are arguing that properly crafted legislation can also provide such pressure.
In the early days of OSHA’s regulation of noise exposure, many companies made considerable efforts to find ways to reduce noise levels, and trade associations conducted noise studies on behalf of their members. However, when OHSA compliance officers began citing companies for not having engineering controls in place, company attorneys turned the noise exposure questions into legal ones. Companies contended that economic feasibility was important and that engineering controls had to be both technically and economically feasible. The Occupational Safety and Health Review Commission (OSHRC), the federal agency that decides disputed citations and penalties issued by OSHA, decided that economic feasibility had to be considered. This decision caused OSHA to slow down on its citations and many companies to sue before OSHRC rather than pay penalties. For sample cases, see OSHRC, 2009.10
In 1983, OSHA put forward an enforcement directive (see OSHA, 2009, for the current version) setting a 100-dB action point for requiring engineering control of noise as long as workers’ hearing was adequately protected by HPDs. This weak enforcement policy signaled the death knell for the engineering control of noise in all but the most progressive and innovative companies. As a result, original equipment manufacturers no longer had an incentive to manufacture quiet products because there was no more market for them in the United States.
“BUY QUIET” PROGRAMS
In general, retrofitting existing machinery for noise suppression, especially if it has already been installed in the workplace, can be very expensive. Even though many large manufacturers are acutely aware of the noise problem created by their equipment, many companies adopt hearing conservation programs in lieu of engineering controls.
There is some pressure, however, for companies to purchase quieter equipment. For example, EU regulations specify noise emission limits for many kinds of outdoor equipment. In addition, the Physical Agents Directive (EC, 2003) sets limits for workplace noise levels lower than the limits in the United States. In addition, one industry, the information technology industry, has requirements for noise emissions from their products defined by the Swedish government and spelled out in a Swedish standard (Statskon-toret, 2004). Many purchasers of equipment—for example, in the automotive and oil refining industries—also have noise specifications for new equipment. Thus, U.S. companies that want to sell their products or equipment in the European market must meet these standards.
The federal government has the authority to purchase low-noise products (42 USC 65, Section 4914, Development of Low-Noise-Emission Products), and NIOSH and NASA both promote “buy quiet” programs and specifications for low-noise products.
NIOSH is involved in a number of efforts to promote noise declarations that can facilitate the implementation of buy-quiet programs.11 One works within existing hand-arm vibration efforts by the U.S. Army, U.S. Navy, NASA, and the General Services Administration. The groups are collaborating to develop and disseminate a database of equipment sound and vibration exposure levels. This work includes vetting equipment through GSA acquisition channels for implementation throughout the Department of Defense. Additionally, the effort may persuade machinery and equipment manufacturers to make reduced noise a marketing feature and invest in developing, testing, and selling quieter products. NIOSH is also working to translate research on sound levels and engineering noise controls into practical information by making a revised NIOSH Noise Control Compendium
10 |
Occupational Safety and Health Review Commission (OSHRC). 2009. For sample cases, see: http://www.oshrc.gov/decisions/html_1978/7855_10561_12069_76-0025.html http://www.oshrc.gov/decisions/html_1983/15647.html http://www.oshrc.gov/decisions/html_1978/13773.html http://www.oshrc.gov/decisions/html_1984/14131.html http://cases.justia.com/us-court-of-appeals/F2/692/641/379249/ |
11 |
Charles Hayden, personal communication, March 17, 2009. |
(NIOSH, 1978) and a revised Compendium of Materials for Noise Control (NIOSH, 1975) available on the Internet. In addition, they are updating and expanding their existing powered hand tool database.
Stringent federal noise regulations in the mining industry have led to successful noise control collaborations between NIOSH and mining machinery manufacturers. Mining companies are committed to “buy quiet,” and machinery manufacturers are amenable to any collaborative effort to assist them in reducing noise levels from their products. Similarly, noise regulation outside of mining would greatly assist in creating an environment of collaboration and openness to reduce levels, for example, in the construction industry (Hayden and Zechmann, 2009).
In 1996, NASA implemented a “buy quiet” program (Cooper and Nelson, 1996). The program was updated and reviewed in 1999 (Cooper et al.) and described in detail at the INTER-NOISE conference in 2009 (Cooper, 2009).
“Buy quiet” programs and a new “buy-quiet” criterion for industrial equipment have also been reviewed by a member of the NAE study committee, Robert D. Bruce (2009). He described how one global company had set a criterion of 80 dB(A) at 1 meter as the purchase requirement for new equipment. However, he said, this specification cannot stand alone; it must be accompanied by information about the acoustical environment, measurement locations, and machine operating conditions. Bruce also described how new equipment should be installed in existing facilities.
Buying and Selling Low-Noise Equipment
When considering the cost of purchasing quieter equipment, the potential buyer must take into consideration the costs of a long-term hearing conservation program for workers in environments with hazardous noise levels. Hearing conservation programs incur costs for annual audiometric monitoring, medical follow-up of hearing loss cases, monitoring of noise exposure, posting of warning signs and controlling access to high-noise areas, annual training for employees and supervisors, recurring purchases of personal hearing protectors, ongoing administration and record keeping, and inevitable workers’ compensation claims for hearing loss.
Even if the buyer has made the decision to proceed, specifying a limit for the noise emissions of a product can be difficult. First, neither the seller nor the purchaser may be familiar with noise emission specifications. Second, the type of specification varies with the type of equipment, and the specification must be meaningful to the seller. For example, a specification such as “must meet OSHA requirements” is not adequate. If a manufacturer relies on vendors to supply subassemblies, the manufacturer/vendor relationship may be complicated. In addition, small vendors usually do not have the facilities to determine the noise emissions of components and subassemblies. Another complication is that the noise emitted by a machine may depend on the work being done, for example, when forming metal. The manufacturer may control the noise of motors, cooling equipment, etc., but the buyer must take some responsibility for the noise or the operating conditions of the machine must be very carefully specified when the noise emission levels are specified. Thus, manufacturer and buyer must work together closely to produce a satisfactory design.
Nevertheless, there are several good reasons for a buyer and seller to come to agreement on a noise specification:
-
In areas with hazardous noise levels, the noise hazard can be reduced, saving the costs of a hearing conservation program.
-
Speech communication in low-noise workplaces is much better than in high-noise workplaces. In addition, because no hearing protection is necessary, desired sounds, such as announcements via public address systems, are not attenuated.
-
Low-noise workplaces promote safety (e.g., alarms are clearly audible).
-
Low-noise workplaces make it easier for workers to concentrate and reduce fatigue.
-
Low-noise workplaces are more productive and more comfortable.
Generally, low-noise equipment is easier to maintain than retrofitted equipment, and controls are easier to use. Although the energy radiated as noise is a very small fraction of the electrical or mechanical energy in any process, a low-noise machine is usually thought of as being more energy efficient and of good design. Guidelines for low-noise design can be found in international documents (ISO, 1995b, 1998).
Responsibilities of Buyers and Sellers
Both supplier and purchaser have responsibilities in implementing a “buy quiet” program. For individual pieces of machinery, such as compressors, motor generators, and similar equipment, the supplier must make available the noise specification for the equipment, usually in terms of the sound power level it emits. Several sets of standards have been established for determining sound power. For example, the International Organization for Standardization (ISO) has generic standards for noise emissions. In addition, many other international standards have been developed for noise emissions from specific kinds of equipment.12 Other industry standards and other national standards may also be used. For example, ANSI Standard S12.15-1992 (R 2007) defines microphone positions and other information to determine noise emissions for a wide variety of equipment (ANSI, 2007a). In addition, ANSI S12.16-1992 (R 2007) provides information
12 |
See Chapter 6 and Appendix C for more on ISO standards and other international standards. |
on how to request noise emission data for machinery and equipment (ANSI, 2007b).
A variety of standards for noise emitted by household appliances have been published by the International Electro-technical Commission (IEC, 2010). Information on preparing specifications and recommended noise emission levels for equipment that will be used in classrooms has also been published (Hellweg et al., 2006).
An alternative to a sound power level specification is an emission sound pressure level specification. Methods of making these measurements are described in international standards. The basic guidelines can be found in ISO 11200:1995 (ISO, 1995a), and the series is listed in the ISO Standards Catalog.
The relationship between sound power level (emission) and sound pressure level (immission) is discussed in most handbooks and is discussed in this report in Appendix A. Emission sound pressure level specifications cover the relationship between the two quantities for a diffuse field in a room and show, for a given amount of sound absorption, how sound decreases as one moves away from a noise source. Other examples of this relationship are techniques used in the information technology industry to calculate noise levels in a space with large numbers of machines (ECMA International, 1995).
In settings where a large number of pieces of equipment are on a manufacturing floor, the purchaser and supplier must work together to define noise emission specifications tailored to the specific pieces of equipment being purchased. The purchaser must translate the desired noise immission level in a given environment to a noise emission level that can be understood and validated by the manufacturer. The noise emission of equipment is generally specified in terms of sound power or emission sound pressure, whereas immission, the level measured in the workplace, depends on the number of machines in a given area, the size and shape of the space, the amount of sound absorption, and the scattering of sound from one or more machines. Thus, the connection between emission and immission must usually be resolved by a professional in noise control engineering who can define the relationship between the noise emission of equipment and the noise levels in the manufacturing environment. The purchaser can then determine whether or not a noise problem exists. A workplace with a sound pressure level of 75 dB(A) for an 8-hour exposure is generally considered safe but unpleasant. Levels of 80 dB(A) and higher raise concerns about damage to workers’ hearing.
HEARING PROTECTION DEVICES
The First Hearing Protectors
HPDs, which protect the human ear from incurring NIHL, have been in existence at least since the early 1900s, although their use in U.S. workplaces was not regulated by law until 1971. In fact, in 1911 the famous band leader John Phillip Sousa complained to his friend and fellow skeet trapshooter J. A. R. Elliott that shooting traps “took a toll on his ears and was beginning to affect his livelihood [as a musician].” Elliott, an inventor, then developed and patented (in eight countries), the “Elliott Perfect Ear Protector,” which became a commercial success. After using the Elliott Protector, Sousa wrote a letter to Elliott on January 20, 1913: “I consider your invention to lessen the shock of loud noises or overwhelming vibrations of sound of great comfort. The Elliott Perfect Ear Protector is a great success in affording protection from concussions to a sensitive ear. As a shock absorber it is invaluable” (Baldwin, 2004).
Unfortunately, although simple cotton plugs were known to be used in some workplaces before the turn of the 19th century (e.g., Barr, 1896), U.S. industrial workers did not routinely use effective HPDs until many years later. The lack of protection, coupled with high noise exposures, resulted in NIHLs and related problems, such as tinnitus, which were often viewed as accepted consequences of one’s occupation. Terms such as “blacksmith’s deafness” and “boilermaker’s ear” were coined to describe these common afflictions (Fosboke, 1831; Holt, 1882).
Hearing Protection in the Military and Industry
In the first half of the twentieth century, HPDs were not commonly used in U.S. workplaces or for most leisure-time exposures. However, the U.S. military has recognized their importance at least since World War II for protecting against the effects of noise-emitting ordnance, as well as loud machinery, such as tanks and aircraft. In fact, one of the earliest regulations on hearing conservation was U.S. Air Force Regulation 160-3 of 1948 (Department of the Air Force, 1948), which called for the use of HPDs. In U.S. workplaces, however, although a few industrial hearing conservation programs appeared in the 1940s and 1950s (Berger, 2003b), hearing protection was not required by law until May 1971, with promulgation of the Occupational Noise Exposure Standard under the authority of the Occupational Safety and Health Act. This was the first requirement, based on exposure levels, for hearing protection in general manufacturing industry (OSHA, 1971a); a similar law was promulgated for construction workers (OSHA, 1971b), industry and construction being the settings where the U.S. workers were, and continue to be, most at risk for NIHL.
Later, in 1981, the legal advent of the OSHA Hearing Conservation Amendment for General Industry (OSHA, 1981) immediately caused the use of HPDs to proliferate in U.S. industrial workplaces. The amendment required that employers provide a choice of HPDs to any worker exposed to noise of 85-dB(A) time-weighted average (TWA), or 50 percent noise dose, for an 8-hour workday, with the
measurement taken on the “slow” scale of the sound-level meter and using a 5-dB exchange rate between exposure dB(A) level and time of exposure.
Other industries, including airlines, truck and bus carriers, and railroads, have separate, generally less comprehensive, noise and hearing conservation regulations. Unfortunately, to date, no analog to the OSHA Hearing Conservation Amendment of 1981 has been adopted into law, although in 2002 OSHA issued an advance notice of proposed rulemaking for the construction industry (Federal Register, 2002) where noise levels can also be hazardous (Casali and Lancaster, 2008). Workers in agriculture and oil and gas drilling are not covered by noise regulations.
In the mining industry, hearing protection has been addressed, first under the Federal Coal Mine Health and Safety Act of 1969 and later under the Federal Mine Safety and Health Amendments Act of 1977. In 1999 the MSHA issued a more comprehensive noise regulation governing all forms of mining (MSHA, 1999). The regulation emphasized engineering control but did include the use of HPDs.
The major point about all of these historical milestones in federal regulatory development is that hearing protectors were not really addressed in U.S. occupational safety and health law until the late 1960s and early 1970s.
Hearing Protection Outside the Workplace
Although data on the use of HPDs outside the workplace are elusive, there are indications that they are becoming more popular as awareness of NIHL increases. HPDs can protect hearing from hazardous noises produced by some power tools, lawn care equipment, recreational vehicles, target shooting and hunting, spectator events, amplified music, outdoor construction equipment, and many other sources. In fact, some of these activities, such as using recreational firearms (Nondahl et al., 2000) and attending motorsport events, such as monster truck races (Casali, 1990), pose the risk of exposure to noise levels equal to, or even beyond, the levels experienced by workers in many industries. HPDs can reduce the energy to the ear from these noises and prevent hearing loss.
HPDs can also be beneficial in noisy environments that pose no real threat to hearing. For example, HPDs can reduce noise annoyance in passenger cabins of commercial aircraft and on subways and buses. They can also reduce noise in sleeping environments, such as traffic noise or snoring (although HPD use while sleeping is not recommended because it can interfere with the audibility of acoustic signals such as smoke alarms, telephones, and doorbells).
Hearing protection features are also incorporated into other products worn on the ears, such as headphones worn by music lovers and headsets worn by crew members for cockpit communications. Some hearing protection features can improve the fidelity of audio signals and the intelligibility of speech. Thus, an effective headphone/headset can not only improve the signal/speech-to-noise ratio but can also protect against the hazards of ambient noise.
When using HPDs, particularly earphones for listening to music or speech, wearers must understand that external signals, such as sirens or stall warnings in an aircraft cockpit, might be attenuated or even masked completely. The effects of headphones/headsets on the situational awareness of the wearer depend on the particular situation, the individual user, and the design of the HPD (e.g., the frequency spectrum of attenuation produced by passive and/or active noise cancellation features).
HEARING PROTECTION VERSUS (OR AS AUGMENTATION OF) ENGINEERING NOISE CONTROL
Systems Approach
In a straightforward systems approach to noise abatement, efforts to reduce or eliminate noise exposures are concentrated in three primary locations: the noise source, the sound propagation path, and the receiver (see Figure 4-1). From a systems perspective, HPDs are the last line of defense in the protective chain (Berger, 2003b; Casali, 2006; Gerges and Casali, 2007). This is because an HPD may not always be effective; it is an active countermeasure implemented at the receiver, who must use it properly, as opposed to a passive countermeasure, such as engineering controls that are implemented at the noise source or ini ts propagation path. Like a seatbelt, an HPD requires that a person use it at the right time and use it properly to provide protection (see Figure 4-2). Like a crashworthy design, the performance of an engineered noise control device does not depend on human behavior.
There are several other reasons for using a passive countermeasure:
-
It is the employer’s duty according to the Occupational Safety and Health Act of 1970 to provide a safe and

FIGURE 4-1 Systems approach to reducing noise exposures.
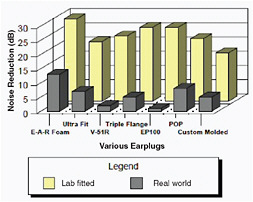
FIGURE 4-2 Comparative noise reduction ratings for various earplugs. Source: NIOSH, 1996.
-
healthy workplace, not the employee’s duty to provide that protection.
-
Hearing protectors often provide insufficient attenuation.
-
Hearing protectors are often uncomfortable and therefore not accepted by workers.
-
Hearing protectors are often counterproductive in that they reduce the worker’s ability to hear speech communication and warning signals.
-
Hearing protectors can have an adverse effect on the ability to localize sounds and therefore pose a safety hazard.
The focus of noise reduction efforts should certainly be on the development and purchase of quieter consumer products and industrial machinery and on reducing noise via engineering controls at the noise source or in the noise path. However, when engineering controls are not economically or technically feasible, or when an employer or manufacturer (unfortunately) does not consider them a high priority, hearing protection may supplant engineering and/or administrative controls (e.g., setting time limits to a worker’s exposure).
For these reasons the use of HPDs has proliferated, especially in industrial and military settings. In situations where it is difficult, or even infeasible, to “engineer out” noise, such as that from weapons or aircraft, HPDs may be the only practical countermeasure. In addition, there are some cases in which engineering and/or administrative controls have been implemented but do not reduce the noise to an acceptable (or even legal) level. In these situations, HPDs may be used to “make up the difference” and protect against NIHL.
Limitations of Hearing Protection Devices
If exposures to noise at hazardous levels persist even after noise controls have been tried, HPDs may be the only way to protect hearing. Permanent NIHL is typically a progressive neural injury that damages or destroys the hair cells and neural pathways of the inner ear. However, NIHL can also be an immediate response to an acoustic trauma if the elastic limits of the tympanum, ossicular chain of the middle ear, or cochlear structures are overwhelmed by a powerful acoustical insult, such as an explosion. For the great majority of noises to which people are exposed, HPDs can mitigate NIHL, provided they are properly selected, fitted, and worn.
In industry, where 90 percent of noise exposures are at TWA levels less than or equal to 95 dB(A), compliance with the OSHA 1983 Hearing Conservation Amendment requires only a 10-dB reduction, which most HPDs can supply (Berger, 2003b). However, HPDs are not a panacea. They may be ineffective if the acoustical pathways, such as air leaks around the seal, HPD material transmission, HPD vibration, and flanking via bone conduction interfere with their noise reduction features. In addition, though rare, extremely high noise levels may overwhelm the attenuation capabilities of even the best HPDs. For example, for 8-hour daily TWA exposures that exceed about 105 dB(A), especially with dominant low-frequency content below about 500 Hz, double passive hearing protection (i.e., an earmuff worn over a well-fitted earplug) is advisable (Berger, 2003b). However, because of such factors as discomfort and concerns about safety, workers often complain about wearing even one earmuff or earplug, and convincing them of the necessity of wearing both during the course of a workday can be a challenge.
In even more severe noise environments, such as on aircraft carrier decks during flight operations, prevailing noise exposures can be extremely high, and short-term levels may range from 146 to 153 dB(A) at 50 feet from military jet aircraft on afterburner power (McKinley, 2001). These levels will overtax even the double passive HPDs. In those cases very specialized HPDs are required and are mainly of interest only in military applications. These devices are described briefly in the section on multicomponent systems for extreme noise later in the chapter.
Hearing Protection Devices in Nonoccupational Settings
Home and Recreational Use
In contrast to the use of HPDs in most occupational settings in the United States, the use of HPDs in recreational and home settings is generally up to the individual—and in most cases depends on awareness of what constitutes unsafe noise and a person’s willingness to take risks. Despite programs to educate people about noise-related dangers and the importance of HPDs, public awareness about the hazardous effects of noise is low (ASHA, 2009; WHO, 1997).
In addition to conventional passive hearing protectors, which have been available for decades, HPDs styled and sized specifically for children, designed for spectator events (e.g., earmuffs that incorporate radios for sporting events),
HPDs with signal pass-through circuitry (e.g., electronic earmuffs for hunters), lightweight active noise cancellation HPDs for reducing low-frequency noise in aircraft cabins, uniform attenuation earplugs for musicians and concert attendees, and other innovative and attractive devices are now on the market.
Local Ordinances on Hearing Protection
In contrast to long-standing federal laws for occupational exposures, noise in community and recreational settings, if governed at all, is usually addressed in local ordinances, most of which relate to noise annoyance rather than to hearing risks. However, in venues having recreational exposures from amplified music, or gaming arcades, there may be warning signs stipulating that hearing protection is required upon entry. However, ordinances to protect hearing are in the minority, often passed in response to public complaints and/or civil litigation for premises’ liability. Again, the committee questions why noise is not controlled to within safe limits by engineering means or by “turning down the volume,” rather than by warning people to wear hearing protection and depending on them to have such protection at hand.
HEARING PROTECTION DEVICES: TECHNOLOGIES AND EFFECTS ON AUDIBILITY
Conventional (Passive) Hearing Protection Devices
The vast majority of HPDs are so-called conventional hearing protectors that attenuate noise by static passive means. Conventional, or passive, HPDs do not havedynamic mechanical elements, such as valves or reactive ports, or electronic circuitry, such as active noise cancellation or signal pass-through circuitry. The effectiveness of passive HPDs depends on a combination of acoustical factors, including the airborne sound transmission loss imposed by the construction materials, the reflection characteristics of the HPD for incident sound waves, the quality and integrity of the seal against the ear canal or outer ear or its surrounding tissue, the ability of the HPD to dampen vibrations of the ear canal wall, and the resonance frequency characteristics and acoustical impedances of the HPD. There are four general types of conventional HPDs—earplugs, semi-insert or ear canal caps, earmuffs, and helmets—each defined by the way the device interfaces with the ear or head.
Earplugs are vinyl, silicone, spun fiberglass, cotton/wax combinations, or closed-cell foam products inserted into the ear canal to form a noise-blocking seal. Proper fit to the user’s ears and training in insertion procedures are critical to their effectiveness. A related, but different, category of HPD is the semi-insert or ear canal cap, which consists of an earplug-like pod positioned at the rim of the ear canal and/or in the concha bowl of the external ear (pinna). The device is held in place by a lightweight headband positioned under the chin, behind the head, or over the head. The headband of an ear canal cap can also be used to store the device around the neck when not in use.
Earmuffs are ear cups, usually made of a rigid plastic material with a noise-absorptive liner, that completely enclose the outer ear and seal around it with foam- or fluid-filled cushions. On some models the headband that connects the ear cups is adjustable so that it can be worn over the head, behind the neck, or under the chin, depending on the presence of other headgear, such as a welder’s mask. Helmets, which enclose a large portion of the head, are usually designed to provide impact protection, but they can have integrated ear cups or a liner material that seals around the ears (Berger and Casali, 1997). Furthermore, for extreme noises that substantially transmit sound through bone conduction to the neural ear, helmets that cover the temporal and mandibular areas, as well as the cranium, can provide additional protection against bone-conducted noise (Gerges and Casali, 2007).
In general, earplugs provide better attenuation than earmuffs for noise below about 500 Hz and equivalent and better protection for sounds above 2,000 Hz. At intermediate frequencies, earmuffs generally provide better attenuation. Earmuffs are generally easier than earplugs or ear canal caps for the user to fit properly. However, in high temperatures and humidity, earmuffs can be uncomfortable; in cold temperatures they can be welcome insulators. Semi-inserts generally provide less attenuation and are more uncomfortable than earplugs or earmuffs. However, because they can be stored around the neck, they are convenient for workers who frequently move in and out of noisy areas. For a comprehensive review of conventional HPDs and their applications, see Gerges and Casali (2007) and Berger (2003b).
Although conventional HPDs provide adequate protection for most noise exposures, a potential disadvantage, due to the static, passive nature of the attenuation, is a deleterious effect on hearing quality and auditory performance. This effect varies with the user’s hearing ability and the noise and signal conditions. For more specific information on the effects of HPDs on speech communication and signal audibility, the reader is referred to Casali (2006), Robinson and Casali (2003), and Suter (1992).
HEARING PROTECTION DEVICES: EFFECTS ON SIGNAL AND SPEECH AUDIBILITY
Overprotection Versus Underprotection
Safety professionals must select HPDs for the workplace that provide adequate attenuation for the noise threat but not so much attenuation that the worker cannot hear important signals and/or speech communications. Users may reject an HPD if it compromises hearing to the point that sounds seem unnatural, signals are undetectable, and/or speech is not understandable. Too much attenuation for a particular noise situation is commonly referred to as overprotection.
The selection of an overprotective or underprotective HPD can have serious legal ramifications. Here is a hypo-
thetical statement by a workers’ compensation plaintiff: “The hearing protector provided inadequate noise attenuation for defending my ears against the damaging effects of noise, so I lost my hearing over time.” Also: “The hearing protector provided more attenuation than needed for the noise I was exposed to at work, and therefore was a causal factor in the accident when I could not hear the forklift backup alarm and was run over.”
These are extreme examples, but in civil court such arguments can potentially lead to theories on which a legal foundation for recovery of damages may be based. Consider product liability, for example. The “failures” claimed in the statements above would typically fall under the category of defective design and/or availability of superior alternative design features, and/or breach of warranty. The threat of litigation is of great concern to both HPD manufacturers and employers. Thus, HPDs must be matched to workers and job requirements. The above paragraphs lend even more support to the principle that engineering noise controls should have priority over HPDs.
Effects on Audibility Leading to Technological Augmentations
Research on people with normal hearing suggests that conventional passive HPDs have little or no degrading effect on their understanding of external speech or signals in ambient noise levels above about 80 dB(A); they may even provide some improvements, with a crossover from disadvantage to advantage between 80 and 90 dB(A) (Berger and Casali, 1997; Casali and Gerges, 2006). However, in lower sound pressure levels, they often do increase misunderstanding and poorer detection. In these situations, HPDs are usually used not to protect hearing but to reduce annoyance. In the presence of intermittent noise, HPDs may be worn during quiet periods so that when a loud noise occurs, the wearer will be protected. However, during the quiet periods, hearing acuity may be reduced.
Technological enhancements are sometimes incorporated to create level-dependent augmented HPDs that provide minimal or moderate attenuation (or sometimes more amplification of external sounds) during quiet times and increased attenuation (or less amplification) as the noise level increases. However, commercially available versions of these devices have not been associated with a demonstrated improvement in signal detection over conventional HPDs in most situations (e.g., Casali and Lancaster, 2008; Casali and Robinson, 2003).
Noise- and age-induced hearing losses generally occur in the high-frequency range first, making it difficult to determine the effects of HPDs on speech perception for people with early impairment. Because their elevated thresholds for mid- to high-frequency speech sounds are elevated further by the protector, hearing-impaired individuals are usually disadvantaged by conventional HPDs. Comprehensive reviews (e.g., Suter, 1992) have concluded that people with sufficient hearing impairments usually experience additional reductions in communication abilities with conventional HPDs in noisy environments.
Moreover, because of the phenomenon known as the occlusion effect, people who wear HPDs lower their voices by about 2 to 4 dB, so that when both talker and listener wear protectors, the resulting decrease in speech recognition will tend to offset any benefits, even with normal-hearing listeners (Howell and Martin, 1975; Hoermann et al., 1984).
HPDs with electronic hearing-assistive circuits, sometimes called electronic sound transmission or sound restoration HPDs, can be offered to hearing-impaired individuals to determine if their hearing, especially in quiet-to-moderate noise levels below about 85 dB(A), can be improved and their hearing still somewhat protected. However, the benefits of electronic sound transmission HPDs for hearing-impaired users have not been empirically demonstrated in scientific studies.
Nonlinear Passive Attenuation
Conventional passive HPDs cannot selectively relay speech or nonverbal signals (or speech) energy rather than noise energy at a given frequency. Therefore, conventional HPDs do not improve the speech/noise ratio in a given frequency band, which is the most important factor for achieving reliable signal detection and speech intelligibility. As shown in Figure 4-3, conventional earplugs (labeled fiberglass, premolded, or foam) attenuate high-frequency sound substantially more than low-frequency sound; therefore, they attenuate high-frequency consonant sounds, which are important for word discrimination. They also attenuate frequencies that are dominant in many warning signals. This nonlinear attenuation profile, which generally increases with frequency for most conventional earplugs and nearly
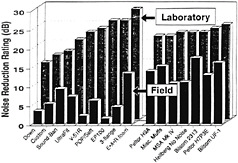
FIGURE 4-3 Comparative noise reduction ratings based on manufacturers’ laboratory tests and real-world “field” performance of different types of hearing protection devices. Adapted with permission from Berger, 2003b, Fig. 10.18, p. 421.
all conventional earmuffs, allows more low-frequency than high-frequency noise through the protector, which causes an “upward spread of masking” if the penetrating noise levels are high enough (Robinson and Casali, 2003).
Certain augmented HPD technologies help overcome these weaknesses, particularly low-frequency attenuation. These include a variety of active noise reduction (ANR) devices that capture the offending noise and its electronic phase cancellation at the ear via superposition through feedback and/or feed-forward control loops. ANR devices boost low-frequency attenuation below about 1,000 Hz. ANR is especially effective in earmuffs, which are generally weakest in low-frequency attenuation and which also have enough space for the electronics of ANR circuitry to be packaged in/on the muff. ANR has also been used in earplug designs in the past decade (e.g., McKinley, 2001). The benefits of ANR-based HPDs can include reduction of upward spread of masking of low-frequency noise into the speech and warning signal bandwidths and reduction of noise annoyance in environments dominated by low-frequency noise, such as jet cockpits and passenger cabins (Casali and Robinson, 2003).
The tendency of conventional HPDs to exhibit a sloping nonlinear attenuation profile with changes in frequency creates an imbalance from the listener’s perspective because the relative amplitudes of different frequencies are heard differently than they would be without the HPD. Thus, broadband acoustic signals are heard as spectrally different (more “bassy”) from normal acoustic signals (Berger, 2003b).
People whose jobs depend on accurate sound interpretation (aural inspections by machinists, miners, engine troubleshooters), as well as people who perform or listen to music, may be adversely affected. Figure 4-4 shows attenuation curves for two uniform (or flat) attenuation devices (ER-15 and ER-20). These devices are more popular with musicians than conventional HPDs because they do not distort perceptions of the loudness of various pitches (Casali and Robinson, 2003).
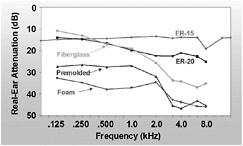
FIGURE 4-4 Spectral attenuation obtained with real-ear attenuation at threshold (REAT) procedures for three conventional passive earplugs (premolded, user-molded foam, and spun fiberglass) and two uniform-attenuation, custom-molded earplugs (ER-15, ER-20). Provided courtesy of E.H. Berger, AEARO—3M.
Some high-frequency binaural cues (especially above about 4,000 Hz) that depend on the external ears (pinnae) are altered by HPDs, compromising judgments of sound direction and distance. Earmuffs, which completely obscure the pinnae, may interfere with localization in the vertical plane and may also cause horizontal-plane errors in both contralateral (left-right) and ipsilateral (front-back) judgments (Suter, 1992). Earplugs may cause some ipsilateral judgment errors but generally cause fewer localization errors than earmuffs because they do not completely destroy cues from the pinnae.
Dichotic sound transmission HPDs compensate for lost pinnae-derived cues. These devices have an external microphone on each earmuff cup that transmits a specified passband of the noise incident on each microphone to a small loudspeaker under the earmuff cup. Binaural cues are thus maintained, as least partly, as long as the between-ear gain controls are properly balanced, the microphones are sufficiently directional, and the passband includes frequencies outside the range that cannot be typically localized (i.e., outside the range of about 1,000 to 3,000 Hz). However, a recent experiment with a dichotic sound transmission earmuff in an azimuthal localization task of determining the approach vector of a vehicular backup alarm demonstrated no advantage in localization over a conventional earmuff or earplug (Casali and Alali, 2009).
All of the augmentations described above—uniform attenuation, ANR, electronic sound transmission, and level-dependent or amplitude-sensitive attenuation—are effective in certain applications. For more information on these and other technologies that are commercially available, the reader is referred to a review by Casali and Robinson (2003). The major goals of these augmentations are (1) to encourage the use of hearing protection by producing HPDs that are more acceptable to the user population, amenable to the working environment, and adjustable to the noise exposure and (2) to improve hearing in a protected state, which may also make workers safer. Unfortunately, these noble goals are not always realized in practice. One reason is that these devices can be considerably more expensive than conventional passive HPDs, and most employers are reluctant to incur the cost.
EMERGING TECHNOLOGIES
To overcome some of the limitations of HPDs, several recent innovations have been developed or prototyped or in some cases made commercially available. Indeed, emerging technologies continue to be developed. The brief overview that follows includes examples of new technologies known to the committee. However, the list is not exhaustive, and the study committee does not advocate or promote these particular devices or technologies.
Adjustable Attenuation Devices
To “tailor” the attenuation of an HPD to a particular noise problem (i.e., in lieu of selecting different HPDs for different exposures), earplug designs have recently been developed that give the user some control over the amount of attenuation. These devices incorporate a leakage path that can be adjusted via a valve that obstructs a tunnel, or “vent,” cut through the body of the plug (e.g., a Dutch earplug, the Ergotec Varifone) or by selecting a filter or dampers that can be inserted into the vent (e.g., Canadian devices, such as the Sonomax SonoCustom and the Custom Protect Ear dB Blocker).
Verifiable Attenuation Devices
To establish a quality fit of an HPD to a user, and in keeping with the OSHA (1983) Hearing Conservation Amendment requirement, per 29 CFR 1910.95 (i)(5), that “the employer shall insure proper initial fitting and supervise the correct use of all hearing protectors,” several systems have been developed to verify the attenuation of a device worn by a given user. For example, the original SonoPass system, now called the AEARO/3M E•A•RFit, is sold as a system with a probe tube microphone test apparatus that verifies the attenuation level achieved via microphone-in-real-ear, noise reduction measurements on each user as he or she is fitted with the product. A similar system is the Sperian VeriPRO.
All of these verifiable-attenuation HPDs measure attenuation by placing a microphone or probe tube through a duct that runs lengthwise through an earplug and then measuring noise reduction in a sound field. “Verified attenuation” is thus established for that ducted earplug for that particular fitting on the user. Thereafter, for use in the field the ducted earplug is replaced with a solid (i.e., nonducted) earplug of the same type/model; alternatively, a noise-blocking insert is used to occlude the duct. The attenuation achieved by these systems is not recognized by OSHA as a means for determining the adequacy of the hearing protector for a given noise exposure, and it does not replace the EPA-required label of HPD attenuation data. However, with policy amendments, it may someday be recognized for either or both of these applications.
Devices with Enhanced Situational Awareness and Communication Capabilities
In the past few years several HPD-based devices have been developed that have multiple objectives, which include hearing protection from continuous noise, hearing protection from impulsive noise (particularly gunfire), measurement of protected noise exposure (i.e., at the ear under the HPD), improved hearing of ambient sounds and uttered speech, and improved communication capabilities. All of these products incorporate sound transmission circuitry to transduce ambient sounds via a microphone on the outside of the HPD; those sounds are then bandpass filtered to an amplified earphone inside the HPD.
Using elements of rapid-response automatic gain control with high pass-through gain capability, these devices can be used as assistive listening devices for military and other applications, as aids in threat detection, and as sound localizers. They can also improve hearing of low-level speech. When gunfire occurs, the amplification rapidly decays, causing the device to quickly revert to a passive hearing protector. These devices typically have more sophisticated and powerful pass-through filtering/gain circuits than industrial versions of sound transmission earmuffs.
Some of these systems incorporate elements that provide two-way communication capabilities, including versions with covert microphones located under the HPD in the ear canal, to pick up the wearer’s voice by bone/tissue conduction. At least one device can transduce the noise level under the HPD, use it to determine cumulative noise exposure, and modulate the system pass-through gain based on these data. Examples of HPDs that provide enhanced situational awareness include the Communications and Enhancement Protection System from Communications & Ear Protection, Inc.; the QuietProby NACRE AS (Norwegian); and the Silynx QuietOPS. Because of their very recent development, some of these devices have not yet undergone experimentation to test their operational performance. Some, however, have already been deployed for use in combat settings. Further discussion of HPDs with situational enhancement, and experimentation on a subset of them, can be found in Casali et al. (2009).
Multicomponent Systems for Extreme Noise
Multicomponent HPD systems have recently been developed and tested for use in noise environments that greatly exceed the attenuation capabilities of even double passive protectors (i.e., earmuffs worn over earplugs). The most prominent of these environments is an aircraft carrier deck during flight operations, where flight deck personnel are subject to sound pressure levels as high as the mid-150-dB(A) range (McKinley, 2001). Some large-caliber weapons and explosive blasts can also produce exceedingly high exposures.
Specialized HPDs have been developed for use in these extreme conditions, including devices with multiple components for staged hearing protection for use on aircraft carriers. These HPDs provide both high passive attenuation through very deep insertion, custom-molded earplugs coupled with active noise cancellation in the in-canal sound field under the earplug, all covered with a tightly fitted earmuff with custom-fitted cushions (McKinley, 2001). Other devices are full-head-coverage helmets with circumaural active noise cancellation earcups inside, all worn over deeply fitted passive earplugs.
Composite Material Devices
A few HPDs have been produced from a combination of materials, typically in sandwich- or concentric-type construction, to take advantage of impedance mismatching (and the resultant attenuation benefit) that occurs with materials that differ in density, elasticity, and other physical parameters. This design practice has long been used in earmuffs, but composite structures in earplugs will require further investigation.
SUMMARY
Hearing protection is a very important component of a hearing conservation program and is currently essential to combating the problem of noise-induced hearing loss. However, there are disadvantages that accompany the use of HPDs, including but not limited to the high cost of certain augmented HPDs that are needed for specialized applications, situation- and user-specific interference with signal detection and speech communications, discrepancies between laboratory ratings and actual field performance of both conventional passive and electronic protectors, and a perception reported by some workers that HPDs may be “unsafe” (Morata et al., 2005). Furthermore, it must be noted that OSHA (1971a, 1971c, 1983) specifically assigns the responsibility for hearing protection to employers, not workers, and thus the performance of the hearing conservation program is largely dependent on employer commitment to exposure measurement, HPD selection, and training of workers to fit and use the devices properly.
Returning to the systems approach to noise abatement shown in Figure 4-1, it is important to reiterate that hearing protection is a noise countermeasure that is only implementable at the very end of the noise propagation chain, that is, at the receiver’s ear. In the great majority of noise exposure situations the priority should be to reduce or eliminate the noise at its source or in its path through engineering controls and not to rely on hearing protection to curb the noise just before it enters the ears. Hearing protection, though effective when selected and applied properly, is not a panacea for combating the risks posed by noise, and its effectiveness will always be dependent on human behavior. It should thus not be viewed as a replacement for noise control engineering. However, in those cases where noise control engineering’s afforded reduction is simply insufficient, or it is truly economically and/or technically infeasible (as perhaps with a personally shouldered, high-caliber weapon), hearing protection devices become the primary countermeasure.
FINDINGS AND RECOMMENDATIONS
Regulatory Changes in Damage Risk Criteria for Hearing
OSHA has promulgated a noise regulation for general industry, 29 CFR 1910.95. This regulation has been in effect since 1971 and calls for employers to use “feasible administrative or engineering controls” for all employees exposed above a daily time-weighted average level (TWA) of 90 dB(A). In 1981 and 1983 OSHA amended the regulation for hearing conservation requiring employers to supply hearing protection devices and other components of the hearing conservation program at and above a TWA of 85 dB(A). Since 1983, workers who have exhibited a “standard” threshold shift in hearing must be required to wear hearing protection devices above a TWA of 85 dB(A); in addition certain follow-up measures must be taken by the employer. The primacy of engineering and administrative controls over the use of hearing protection devices remains in effect, although OSHA has not enforced it in recent years. In practice, employers have often used technical and/or economic infeasibility as a justification for not implementing engineering controls.
In 1983 OSHA issued a policy directive advising its compliance officers not to issue citations to companies with “effective” hearing conservation programs until workers’ TWAs exceed 100 dB(A). This policy still exists in the agency’s Field Operations Manual (OSHA, 2009); however, it has never had the authority of regulation and could be revoked at any time.
The original OSHA noise regulation used an exchange rate of 5 dB per doubling or halving of exposure time, and this rule has not yet been changed, despite recommendations by EPA and NIOSH to change both the exchange rate to 3 dB and the permissible exposure limit from 90 to 85 dB(A). MSHA promulgated a revised noise regulation in 1999 that is similar but not identical to the OSHA regulation, although here the primacy of engineering noise control is clear. The agency discussed the issues of changing from the 5 dB to the more protective 3-dB exchange rate and from the 90-dB(A) permissible exposure limit to 85 dB(A) but failed to do so at the time, although the preamble to the rule stated that “[i]n both cases, the scientific evidence was strong.” Ultimately, the change was not adopted because of significantly increased costs for small mine operators. The 85/3 limits are used by several other U.S. government agencies and are also written into most national and international standards.
The OSHA Field Operation Manual (OSHA, 2009) contains a statement widely known as the “100-dB Directive.” With reference to issuing citations for noise violations, it states that “[h]earing protectors which offer the greatest attenuation may reliably be used to protect employees when their exposure levels border on 100 dB(A).” The effect of this statement has been to negate the well-recognized goal of using engineering controls as the primary means of controlling industrial noise.
Recommendation 4-1: To comply with the recommendation of the National Institute for Occupational Safety and Health, the policy of several other government agencies, and widespread national and international scientific opinion, the U.S. Department of Labor should adopt the
85-dB(A)/3-dB limit for exposure to hazardous noise. This would replace the current 90-dB(A)/5-dB requirement.
Measurement and Evaluation of the Hazard of Impulsive Noise
The peak sound pressure level is currently widely used to determine noise hazard, but recent studies have indicated that the duration of the impulse plays an important role. There is also evidence that impulsive noise and continuous noise can be included in a single measurement of equivalent sound level. The committee concluded that current damage risk criteria in the United States and internationally are inadequate and should be the subject of future research.
Recommendation 4-2: The National Institute for Occupational Safety and Health should be the lead agency and should be tasked by its parent agencies (U.S. Department of Health and Human Services/Centers for Disease Control and Prevention) to develop new damage risk criteria with assistance from the military services that have experience with high-amplitude impulsive noise.
Promoting Engineering Control to Reduce Hazardous Noise
Engineering noise controls provide significant long-term advantages over personal hearing protection. If workplace noise levels are limited by engineering controls, “buy quiet” programs, or other means to a level below the OSHA action level of 85 dB(A) TWA, the need for individual hearing protection devices (HPDs) is obviated from an OSHA standpoint. HPDs may still be desirable for reducing noise annoyance or ensuring that a noise hazard is fully mitigated.
In 42 USC 65, Section 4914, the federal government is required to encourage the procurement of low noise emission products:
(1) Certified low-noise-emission products shall be acquired by purchase or lease by the Federal Government for use by the Federal Government in lieu of other products, if the administrator of General Services determines that such certified products have procurements costs which are no more than 1.25 percentum of the retail price of the least expensive type of product for which there are certified substitutes. (2) Data relied on by the administrator in determining that a product is a certified low-noise-emission product shall be incorporated in any contract for the procurement of such product.
The same principle applies in the consumer setting. Thus, the engineering of quieter products, such as power tools, toys, yard equipment, and recreational vehicles, would reduce the need for and reliance on HPDs. Even though an HPD may protect the wearer’s hearing, it may create hazards if the user is unable to hear approaching vehicles or alarms.
The effectiveness of HPDs depends on human behavior, and the human factor is always a weak link in the “safety chain.” HPDs must be comfortable, easily sized and fitted to the user, and straightforward to meet the hearing-critical needs of a particular job or situation. They must still provide situational awareness (e.g., communication enhancements where needed and attenuation performance labels that reflect the level of protection they provide in actual use). HPD technology has advanced greatly in the past 30 years, but HPD regulations have not kept pace. This discrepancy was recognized in the publication of EPA’s proposed new rules (EPA, 2009), which should be adopted. However, despite the improvements of recent devices, they cannot be considered a substitute for engineering noise control because of the many factors cited above, and their efficacy simply has not been proven. Moreover, this represents an unacceptable shifting of the burden from employer to employee, which is contrary to both the letter and the intent of the Occupational Safety and Health Act of 1970.
Although an HPD is useful when the listener has no control over the noise level and when engineering controls cannot be applied, the committee concluded that engineering controls of noise in the workplace should be the primary method of protecting workers from hazardous noise exposure. Accordingly, the committee recommends the following actions by U.S. government agencies, engineering and trade societies, and other stakeholders to promote the development and use of engineering controls.
Recommendation 4-3: The U.S. Department of Labor should revoke the Occupational Safety and Health Administration (OSHA) “100-dB Directive” of 1983, which effectively raised the action point for engineering control of noise from 90 to 100 dB by allowing the substitution of hearing protectors for noise control up to 100 dB and thereby devastated the market for quiet machinery and equipment. At the same time, OSHA should reconfirm that engineering controls should be the primary means of controlling noise in the workplace.
Recommendation 4-4: The National Institute for Occupational Safety and Health and the U.S. Department of Labor should develop and distribute widely an electronic database of noise control problems, solutions, and materials—taking into account the many handbooks and articles devoted to industrial noise control.
Recommendation 4-5: Engineering societies and trade organizations should develop guidelines for defining the relationship between noise emission specifications in terms of sound power level and/or emission sound pressure level and noise immission levels in industrial situations. They should provide a primer for buyers and sellers of machinery and equipment that includes descriptions of how noise propagates in rooms; how to determine noise from a large number of machines; standards available to manufacturers and others
for measuring noise emissions; and case histories of noise levels measured in insitu environments.
Recommendation 4-6: Government agencies should be instructed by a presidential directive or in congressional report language to show leadership in promoting “buy quiet” activities by developing and implementing programs for the purchase of low-noise products, as required by 42 USC 65, Section 4914. American industry should adopt “buy quiet” programs that require noise emission specifications on all new equipment and “declared values” in purchase specifications.
REFERENCES
AE (Access Economics Pty Ltd). 2006. Listen Hear! The Economic Impact and Cost of Hearing Loss in Australia. Available online at http://www.audiology.asn.au/pdf/ListenHearFinal.pdf.
Altkorn, R., S. Milkovich, and G. Rider. 2005. Measurement of Noise from Toys. Presented at NOISE-CON 05, The 2005 National Conference on Noise Control Engineering, Minneapolis, MN. Available online at http://www.bookmasters.com/marktplc/00726.htm.
AMT (Association for Manufacturing Technology). 2006. ANSI Technical Report for Machines: Sound Level Measurement Guidelines. McLean, VA: AMT.
ANSI (American National Standards Institute). 1974. Method for the Measurement of Real-Ear Protection of Hearing Protectors and Physical Attenuation of Earmuffs. ANSI S3.19-1974. New York: ANSI.
ANSI. 2002. Methods for Measuring the Real-Ear Attenuation of Hearing Protectors. ANSI S12.6-1997 (R2002). New York: ANSI.
ANSI. 2004. Microphone-in-Real-Ear and Acoustic Test Fixture Methods for the Measurement of Insertion Loss of Circumaural Hearing Protection Devices. ANSI S12.42-1995(R2004). New York: ANSI.
ANSI. 2006a. American National Standard Determination of Occupational Noise Exposure and Estimation of Noise-Induced Hearing Loss. S3.44. ANSI S3.44-1996(R 2006). New York: ANSI.
ANSI. 2006b. American National Standard Methods for the Measurement of Impulse Noise. ANSI S12.7-1986 (R2006). Melville, NY. Acoustical Society of America. Available online at http://asastore.aip.org/shop.do?cID=10.
ANSI. 2007a. American National Standards for Acoustics—Portable Electric Power Tools, Stationary and Fixed Electric Power Tools, and Gardening Appliances—Measurement of Sound Emitted. ANSI/ASA S12.15-1992 (R 2007). New York: ANSI.
ANSI. 2007b. American National Standard Guidelines for the Specification of Noise of New Machinery. ANSI/ASA S12.16-1992 (R 2007). New York: ANSI.
ASHA (American Speech-Language-Hearing Association). 2009. Noise and Hearing Loss—Noise Is Difficult to Define! Available online at http://www.asha.org/public/hearing/disorders/noise.htm).
ASTM (American Society for Testing and Materials). 2008. Standard ASTM F963-08E1, Standard Consumer Specifications for Toy Safety. West Conshohocken, PA: ASTM.
Babisch, W. 2008. Road traffic noise and cardiovascular risk. Noise and Health 10(38):27–33. Available online at http://www.noiseandhealth.org/article.asp?issn=1463-1741;year=2008;volume=10;issue=38;spage=27;epage=33;aulast=Babisch;type=0.
Baldwin, D. 2004. The road to yesterday: J. A. R. Elliott, premier trapshooter. Trap and Field (June-July):94–104. Available online at http://www.traphof.org/roadtoyesterday/elliott-JAR.htm.
Barr, T. 1896. Manual of Diseases of the Ear. Glasgow, Scotland: James Maclehose and Sons.
Berger, E.H. 2003a. Noise control and hearing conservation: Why do it? Pp. 2–17 in The Noise Manual, Revised 5th Ed., edited by E.H. Berger, L.H. Royster, J.D. Royster, D.P. Driscoll, and M. Layne. Fairfax, VA: American Industrial Hygiene Association.
Berger, E.H. 2003b. Hearing protection devices. Pp. 379–454 in The Noise Manual, revised 5th ed., edited by E.H. Berger, L.H. Royster, J.D. Royster, D.P. Driscoll, and M. Layne. Fairfax, VA: American Industrial Hygiene Association.
Berger, E.H., and J.G. Casali. 1997. Hearing protection devices. Pp. 967–981 in Encyclopedia of Acoustics, edited by M. Crocker. New York: John Wiley.
Berger, E.H., J.R. Franks, A. Behar, J.G. Casali, C. Dixon-Ernst, R.W. Kieper, C.J. Merry, B.T. Mozo, C.W. Nixon, D. Ohlin, J.D. Royster, and L.H. Royster. 1998. Development of a new standard laboratory protocol for estimating the field attenuation of hearing protection devices, Part III: The validity of using subject-fit data. Journal of the Acoustical Society of America 103(2):665–672.
Bobeczko, M.S. 1978. Noise Control Solutions for Can Manufacturing Plants. Pp. 413–418 in Proceedings of INTER-NOISE 78, The 1978 International Congress on Noise Control Engineering, San Francisco, CA, May. Available online at http://www.noisenewsinternational.net/docs/bobeczko-1978.pdf.
Bobeczko, M., and D. Landwith. 1982. The Evolution of Can Plant Noise Control Technology. Proceedings of INTER-NOISE 82, The 1982 International Congress on Noise Control Engineering, San Francisco, CA, May. Available online at http://www.noisenewsinternational.net/docs/bobeczko-1982.pdf.
Bruce, R.D. 2007. Engineering controls for reducing workplace noise. The Bridge 37(3): 33–39.
Bruce, R.D. 2009. A New Approach to Noise Control in the Workplace. Proceedings of INTER-NOISE 09, The 2009 International Congress and Exposition on Noise Control Engineering, Ottawa, Canada, August 23–26. Available online at http://www.bookmasters.com/marktplc/00726.htm.
Bruce, R.D., and E. Wood. 2002. National Noise Policy on Occupational Health in the U.S.A. National Industrial-Noise-Control Partnerships. Proceedings of INTER-NOISE 2002, The 2002 International Congress and Exposition on Noise Control Engineering, Dearborn, MI, August 19–21. Available online at http://www.bookmasters.com/marktplc/00726.htm.
Brüel, P.V. 1977. Do we measure damaging noise correctly? Noise Control Engineering Journal 8(2):52–60.
Casali, J.G. 1990. Listening closely to the noise of monster trucks. Roanoke Times and World News, March 5, p. A11.
Casali, J.G. 2006. Sound and noise. Pp. 612–642 in Handbook of Human Factors, 3rd ed., edited by G. Salvendy. New York: John Wiley.
Casali, J.G., and S. Gerges. 2006. Protection and enhancement of hearing in noise. Pp. 195–240 in Reviews of Human Factors and Ergonomics, Volume 2, edited by R.C. Williges. Santa Monica, CA: Human Factors and Ergonomics Society.
Casali, J.G., and G.S. Robinson. 2003. Augmented Hearing Protection Devices: Active Noise Reduction, Level-Dependent, Sound Transmission, Uniform Attenuation, and Adjustable Devices—Technology Overview and Performance Testing Issues. EPA Docket OAR-2003-0024. Washington, DC: U.S. Environmental Protection Agency.
Casali, J.G., W.A. Ahroon, and J.A. Lancaster. 2009. A field investigation of hearing protection and hearing enhancement in one device for soldiers whose ears and lives depend upon it. Noise and Health 11(42):60–69.
Casali, J.G., and K. Alali. 2009. Auditory alarm localization (or not): Effects of augmented passive and alarm spectral content. Spectrum 26(Suppl. 1), and CD of the 34th Annual National Hearing Conservation Association Conference, Atlanta, GA, February 12–14.
Casali, J.G., and J.A. Lancaster. 2008. Quantification and Solutions to Impediments to Speech Communication and Signal Detection in the Construction Industry. Technical Report 200803. Department of Industrial and Systems Engineering, Virginia Polytechnic Institute and State University, Blacksburg, April 15.
Cooper, B.A. 2009. Development and Implementation of Policy-Compliant Site-Specific Buy-Quiet Programs at NASA. Proceedings of INTER-NOISE 09, The 2009 International Congress on Noise Control Engineering, Ottawa, Canada, August 23–26. Available online at http://www.bookmasters.com/marktplc/00726.htm.
Cooper, B.A., and D.A. Nelson. 1996. A “Buy Quiet” Program for NASA Lewis Research Center: Specifying Low Equipment Noise Emission Levels. Pp. 465–470 in Proceedings of NOISE-CON 97, The 1997 National Conference on Noise Control Engineering, University Park, PA, June 15–17, 1997. Available online at http://www.bookmasters.com/marktplc/00726.htm.
Cooper, B.A., D.W. Hange, and J.J. Mikulic. 1999. Engineered Solutions to Reduce Occupational Noise Exposure at the NASA Glenn Research Center: A Five-Year Progress Summary (1994–1999). Pp. 1069–1074 in Proceedings of INTER-NOISE 99, The 1999 International Congress and Exposition on Noise Control Engineering. Fort Lauderdale, FL, December 6–8. Available online at http://www.bookmasters.com/marktplc/00726.htm.
CPSC (Consumer Product Safety Commission). 2001a. Consumer Product Safety Alert: “Don’t Let Children Put Caps for Toy Guns in Their Pockets.” Available online at http://www.cpsc.gov/CPSCPUB/PUBS/5009.pdf.
CPSC. 2001b. Text of the Regulation on Noise from Caps. 16 CFR 1500.121. Available online at http://www.cpsc.gov/BUSINFO/label.pdf.
Davis, R.J., W. Qiu, and R.P. Hamernik. 2009. The role of the kurtosis statistic in evaluating complex noise exposures for the protection of hearing. Ear & Hearing 30(5): 28–634.
DEFRA (Department for Environment Food and Rural Affairs). 2009. Estimating Dose-Response Relationships between Noise Exposure and Human Health in the UK. BEL Technical Report 2009-02. Available online at http://www.defra.gov.uk/environment/noise/igcb/healthreport.htm.
Department of the Air Force. 1948. Precautionary Measures Against Noise Hazards. AFR 160-3. Washington, DC: U.S. Air Force.
EC (European Commission). 2003. Directive 2003/10/EC of the European Parliament and of the Council of 6 February 2003, on the Minimum Health and Safety Requirements Regarding the Exposure of Workers to the Risks Arising from Physical Agents (Noise). Available online at http://eur-lex.europa.eu/LexUriServ/LexUriServ.do?uri=OJ:L:2003:042:0038:0044:EN:PDF.
ECMA International. 1995. Technical Report TR27: Method for the Prediction of Installation Noise Levels, 2nd Edition. Geneva, Switzerland: ECMA International. Available online at http://www.ecma-international.org/publications/techreports/E-TR-027.htm.
Eldred, K.M., W.J. Gannon, and H.E. von Gierke. 1955. Criteria for Short Time Exposure of Personnel to High Intensity Jet Aircraft Noise. U.S. Air Force, WADC Technical Note 55-355, Wright-Patterson AFB, OH.
EPA (U.S. Environmental Protection Agency). 1974. Information on Levels of Environmental Noise Requisite to Protect Public Health and Welfare with an Adequate Margin of Safety. Document Number 550/9-74-004. Available online at http://www.nonoise.org/library/levels74/levels74.htm.
EPA. 1979. Noise labeling requirements for hearing protectors. 40 CFR 211. Federal Register 44(190):56130–56147.
EPA. 1981. Noise in America: The Extent of the Noise Problem. Report No. 550/9-81-101. Washington, DC: U.S. Environmental Protection Agency.
EPA. 2009. Workshop on Hearing Protection Devices, Washington, DC, March 27–28. EPA Docket OAR-2003-0024. Available online at www.regulations.gov.
Federal Railroad Administration. Locomotive Cab Noise. 49 CFR 229.121. Available online at http://frwebgate.access.gpo.gov/cgi-bin/get-cfr.cgi?TITLE=49&PART=229&SECTION=121&YEAR=2000&TYPE=PDF.
Federal Register. 2002. Advanced Notice of Proposed Rule Making, Hearing Conservation Program for Construction Workers. Federal Register 67:50610–50818.
Fligor. B.J. 2009. Risk for noise-induced hearing loss from use of portable media players: A summary of evidence through 2008. Perspectives on Audiology 5(1):10–20.
Fligor, B.J., and L.C. Cox. 2004. Output levels of commercially available portable compact disc players and the potential risk to hearing. Ear and Hearing 25:513–527.
Fosboke, J. 1831. Practical observations on the pathology and treatment of deafness, No. II. Lancet VI:645–648.
Gelfand, S.A. 2001. Essentials of Audiology, 2nd edition. New York: Thieme.
Gerges, S., and J.G. Casali. 2007. Ear protectors. Pp. 364–376 in Handbook of Noise and Vibration Control, edited by M. Crocker. New York: John Wiley.
Hayden II, C.S., and E. Zechmann. 2009. NIOSH Power Tools Database. Available online at http://wwwn.cdc.gov/niosh-sound-vibration/.
Hellweg, R.D., Jr., E.K. Dunens, and T. Baird. 2006. Personal computer, printer, and portable equipment noise in classrooms. Noise/News International 14(3):96–100. Available online at http://noisenewsinternational.net/archives_idx.htm.
Hoermann, H., G. Lazarus-Mainka, M. Schubeius, and H. Lazarus. 1984. The effect of noise and the wearing of ear protectors on verbal communication. Noise Control Engineering Journal 23:69–77.
Hohmann, B.W., V. Mercier, and I. Felchin. 1999. Effects on hearing caused by personal cassette players, concerts, and discotheques and conclusions for hearing conservation in Switzerland. Noise Control Engineering Journal 47:163–165. Available online at http://www.incedl.org/journals/doc/INCEDL-home/jrnls/.
Holt, E.E. 1882. Boiler-maker’s deafness and hearing in noise. Transactions of the American Otological Society 3:34–44.
Howell, K., and A.M. Martin. 1975. An investigation of the effects of hearing protectors on vocal communication in noise. Journal of Sound and Vibration 41:181–196.
IEC (International Electrotechnical Commission). 2010. IEC 60704 Series for Determination of Noise from Household Appliances. Available online at http://webstore.iec.ch/webstore/webstore.nsf/mysearchajax?Openform?key=60704&sorting=&start=1.
IEEE (Institute of Electrical and Electronics Engineers). 1969. Technical Committee Report on Recommended Practices for Burst Measurements in the Time Domain. IEEE 265. New York: IEEE.
I-INCE (International Institute of Noise Control Engineering). 1997. Final Report: Technical Assessment of Upper Limits on Noise in the Workplace. Noise/News International 5:203–216. Available online at http://www.noisenewsinternational.net/archives_idx.htm.
IOM (Institute of Medicine). 2005. Noise and Military Service: Implications for Hearing Loss and Tinnitus, edited by L.E. Humes, L.M. Joellenbeck, and J.S. Durch. Washington, DC: National Academies Press.
ISO (International Organization for Standardization). 1995a. ISO 11200, 1995, Acoustics—Noise Emitted by Machinery and Equipment— Guidelines for the Use of Basic Standards for the Determination of Emission Sound Pressure Levels at a Work Station and at Other Specified Positions. Geneva Switzerland: ISO. Available online at http://www.iso.org/iso/iso_catalogue/catalogue_tc/catalogue_tc_browse.htm?commid=48474.
ISO. 1995b. ISO TR 11688-1:1995, Acoustics—Recommended Practice for the Design of Low-Noise Machinery and Equipment—Part 1: Planning. Geneva, Switzerland: ISO.
ISO. 1998. ISO/TR 11688-2:1998, Acoustics—Recommended Practice for the Design of Low-Noise Machinery and Equipment—Part 2: Introduction to the Physics of Low-Noise Design. Geneva, Switzerland: ISO.
ISO. 1999. ISO 1999:1990, Acoustics—Determination of Occupational Noise Exposure and Estimation of Noise-Induced Hearing Impairment. Geneva, Switzerland: ISO.
ISVR (Institute of Sound and Vibration Research). 1997. Noise from Toys and Its Effect on Hearing. Report 5403 R02. Southampton, U.K.: ISVR. Available online at http://www.isvr.co.uk/leisure/toys.pdf.
LHH (League for the Hard of Hearing). 2009. Children and Toys: Noisy Toys. Available online at http://www.lhh.org/noise/children/toys.html.
Liu, Z. 2003. Acoustic Liner and a Fluid Pressurizing Device and Method Utilizing Same. U.S. Patent No. 6,550,574 B2, April 2.
McKinley, R. 2001. Future Aircraft Carrier Noise. Proceedings of the International Military Noise Conference, Baltimore, MD, April 24–26.
Morata, T.C., C.L. Themann, R.F. Randolph, B.L. Verbsky, D.C. Byrne, and E.R. Reeves. 2005. Working in noise with a hearing loss: Perceptions from workers, supervisors, and hearing conservation program managers. Ear and Hearing 26(6):529–545.
MSHA (Mine Safety and Health Administration). 1999. Health Standards for Occupational Noise Exposure; Final Rule. 30 CFR Part 62, 64. U.S. Department of Labor. Available online at http://www.msha.gov/30cfr/62.0.htm.
NASA (National Aeronautics and Space Administration). 2007. Environmental Health. Chapter 4.9 in Occupational Health Program Procedures. Available online at http://nodis3.gsfc.nasa.gov/displayDir.cfm?Internal_ID=N_PR_1800_001B_&page_name=Chapter4.
NIOSH (National Institute for Occupational Safety and Health). 1975. NIOSH Compendium of Noise Control Materials. Publication No. 75-165. June. Atlanta, GA: NIOSH.
NIOSH. 1978. Industrial Noise Control Manual. Publication No. 79-117. Atlanta, GA: NIOSH.
NIOSH. 1996. Preventing Occupational Hearing Loss—A Practical Guide, edited by J.R. Franks, M.R. Stephenson, and C.J. Mercy. Atlanta, Ga.: NIOSH. Available online at http://www.cdc.gov/niosh/docs/96-110/pdfs/96-110.pdf.
NIOSH. 1998a. Basis for the exposure standard. Chapter 3 in Criteria for a Recommended Standard: Occupational Noise Exposure. Publication 98-126. Available online at http://www.cdc.gov/niosh/docs/98-126/chap3.html.
NIOSH. 1998b. Criteria for a Recommended Standard: Occupational Noise Exposure. Publication 98-126. Available online at http://www.cdc.gov/niosh/docs/98-126/.
NIOSH. 2005. NIOSH/NHCA Best-Practices Workshop on IMPULSIVE NOISE. Noise Control Engineering Journal 53(2):53–60.
Nondahl, D.M., K.J. Cruickshanks, T.L. Wiley, R. Klein, B.E.K. Klein, and T.S. Tweed. 2000. Recreational firearms use and hearing loss. Archives of Family Medicine 9(4):352–357.
OSHA (Occupational Safety and Health Administration). 1971a. Hearing Protection (Construction Industry). 29 CFR 1926.101. Federal Register.
OSHA. 1971b. Occupational Noise Exposure (Construction Industry). 29 CFR 1926.52. Federal Register.
OSHA. 1971c. Occupational Noise Exposure (General Industry). 29 CFR 1910.95. Federal Register.
OSHA 1981. U.S. Department of Labor: Occupational Noise Exposure; Hearing Conservation Amendment; Final Rule. Federal Register (46)4078–4179.
OSHA. 2002. Occupational Noise Exposure. 29 CFR 1910.95. Revised. Available online at http://edocket.access.gpo.gov/cfr_2002/julqtr/29cfr1910.95.htm.
OSHA. 2009. Field Operations Manual, Directive #CPL02-00-148 Effective March 3, 2009. Pp. 4-40 and 4-41. Available online at http://www.osha.gov/OshDoc/Directive_pdf/cpl_02_00_148.pdf.
Park, M.Y., and J.G. Casali. 1991. A controlled investigation of in-field attenuation performance of selected insert, earmuff, and canal cap hearing protectors. Human Factors 33(6):693–714.
Passchier-Vermeer, W. 1999. Pop music through headphones and hearing loss. Noise Control Engineering Journal 47:182–186. Available online at http://asastore.aip.org/shop.do?cID=10.
PIRG (U.S. Public Interest Research Group Education Fund). 2005. Trouble in Toyland: 20th Annual Toy Safety Survey. (See “Dangerously Loud Toys” and “Excessively Loud Toys.” Available online at http://toysafety.net/2005/troubleintoyland2005.pdf.
Porter, M.E., and C. van der Linde. 2005. Conception of the environment-competitiveness relationship. Pp. 92–114 in Economics and the Environment, Selected Readings, fifth edition, edited by R.N. Stavins. New York: W.W. Norton.
Price, G.R. 2007. Validation of the auditory hazard assessment algorithm for the human with impulse noise data. Journal of the Acoustical Society of America 122(5):2786–2802.
Ramazzini, B. 1964. Diseases of workers (De morbis artificum, 1713). Trans. Wilmer Cave Wright. New York: Hafner Publishing. Orig. pub. 1713.
Robinson, G.S., and J.G. Casali. 2003. Speech Communications and Signal Detection in Noise. Pp. 567–600 in The Noise Manual, Revised 5th Ed., edited by E.H. Berger, L.H. Royster, J.D. Royster, D.P. Driscoll, and M. Layne. Fairfax, VA: American Industrial Hygiene Association.
Sataloff, R.T. 1993. Occupational Hearing Loss, 2nd edition. New York: Marcel Dekker.
SCENIHR (Scientific Committee on Emerging and Newly Identified Health Risks). 2008. Potential Health Risks of Exposure to Noise from Personal Music Players and Mobile Phones Including a Music Playing Function. European Commission, Brussels, Belgium.
Schwela, D. 2006. Noise of consumer products: Consequences for environmental health. Noise/News International 14:102–111. Available online at http://www.noisenewsinternational.net/archives_idx.htm.
Shampan, J., and R. Ginnold. 1982. The status of workers’ compensation programs for occupational hearing impairment. In Forensic Audiology, edited by M.B. Kramer and J.M. Ambruster. Baltimore, MD: University Park Press.
Statskontoret. 2004. Statskontoret Technical Standard 26:6: Acoustical Noise Emission of Information Technology Equipment. Swedish Agency for Public Management. Available online at http://www.statskontoret.se/upload/2619/TN26-6.pdf.
Suter, A.H. 1990. Popular misconceptions about occupational noise exposure. Proceedings NOISE-CON 90, The 1990 National Conference on Noise Control Engineering, Austin, TX. Available online at http://www.noisenewsinternational.net/docs/suter-1990.pdf.
Suter, A.H. 1992. Communication and job performance in noise: A review. ASHA Monograph No. 28. American Speech-Language-Hearing Association, Rockville, MD.
Suter, A.H. 1993. The relationship of the exchange rate to noise-induced hearing loss. Noise/News International 1:131–151. http://www.noisenewsinternational.net/docs/suter-1993.pdf.
Suter, A.H. 1994. Current Standards for Occupational Exposure to Noise. Presentation at the 5th International Symposium on Effects of Noise on Hearing, Gothenburg, Sweden, May.
Suter, A.H. 2006. Position paper for the International Safety Equipment Association (ISEA). Available from ISEA, 1901 N. Moore St., Arlington, VA 22209.
USARL (U.S. Army Research Laboratory). 2010. Auditory Hazard Assessment Algorithm for Humans (AHAAH). Available online at http://www.arl.army.mil/www/default.cfm?Action=31&Page=343.
WHO (World Health Organization). 1997. Prevention of Noise-Induced Hearing. Report of an informal consultation held at the World Health Organization, Geneva, Switzerland, October 28–30. No. 3 in the series “Strategies for Prevention of Deafness and Hearing Impairment.” Available online at http://www.who.int/pbd/deafness/en/noise.pdf.
WHO. 1999. Guideline Values. Chapter 4 in Guidelines for Community Noise, edited by B. Bergland, T. Lindvall, and D. Schwela. Available online at http://www.who.int/docstore/peh/noise/guidelines2.html; http://www.who.int/docstore/peh/noise/Comnoise-4.pdf.
WHO. 2007. Prevention of Noise Induced Hearing Loss, Report of an Informal Consultation. Geneva, Switzerland: WHO. Available online at http://www.who.int/entity/pbd/deafness/en/noise.pdf.
Zhao, Y-M., W. Qiu, Z. Lin, S-S. Chen, X-R. Cheng, R.I. Davis, and R.P. Hamernik. 2010. Application of the kurtosis statistic to the evaluation of the risk of hearing loss in workers exposed to high-level complex noise. Ear and Hearing 31(4):527–532.